Many farmers will be very aware of the increasing role played by robotic technologies, known as AgTech, within their industry.
Robotic milking systems, slurry scraping and, more recently, feeding systems quickly come to mind in this regard.
All of these innovations are driven by global position system (GPS) navigation systems. This is the same technology that is driving precision fertiliser spreaders and a wide range of other tillage equipment options around the world at the present time.
And there is little doubt that the footprint of robotics will continue to expand within agriculture during the period ahead.
So it may not come as a complete surprise to learn that these same technologies are now being used within the groundcare sector.
A case in point has been the development of automated line marking systems for use on sports’ pitches and running tracks.
AgTech in ground care
South Antrim-based Budore Grounds Services recently invested in the ‘Turf Tank’ automated line marking system.
The business is operated by the McCallin family – Niall and his uncle, Andy.
The Turf Tank robot is a completely automated, line marking system.
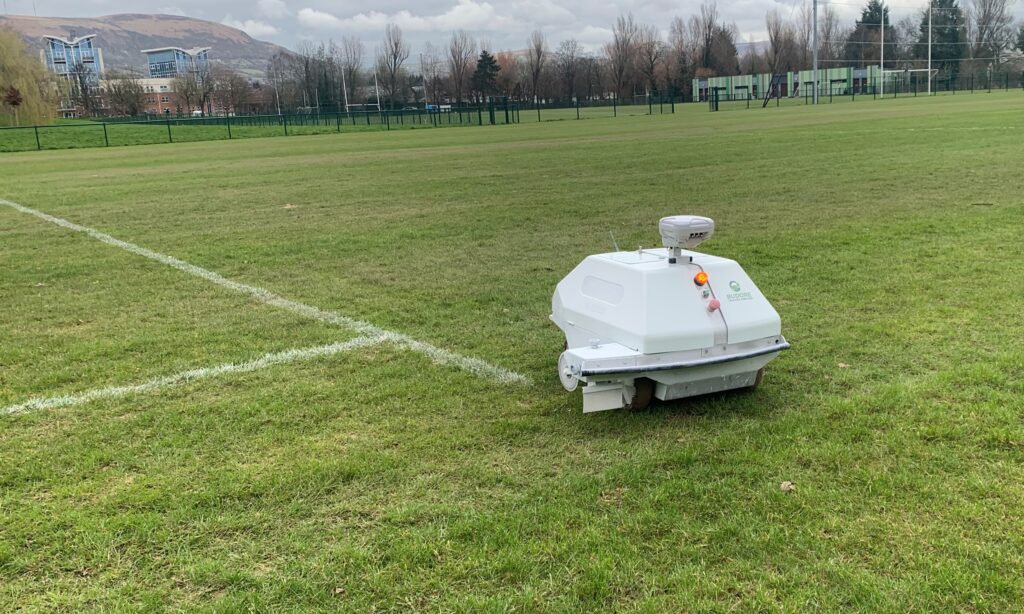
“Due to its GPS technology, the robot eliminates the human error and ensures the lines are marked with maximum precision every time,” Niall explained to Agriland.
“It takes about an hour to map a particular playing field into the computer system.
“After that, the robot takes over. All we need is access to a GPS signal for the accompanying base station.”
According to Andy, it takes the Turf Tank robot approximately one hour to mark out a gaelic pitch.
“Once it starts, I can get on with other jobs,” he added.
“It’s that reliable. We are currently line marking pitches for GAA and soccer clubs. We also mark out running tracks and pitches for a number of universities.
“Many of the clubs use us to precision mark a pitch at the beginning of the season. After that, they can come in with their own, manual equipment as the year progresses.”
The Turf Tank robot sprays a special paint on to the surface to be marked out.
It maintains a consistent speed and spraying pressure for the entire field, which reduces the paint consumption by an average of 50%.
The specification of each job undertaken is retained in the robot’s memory. This means that a field can be line marked whenever required, following a simple, five-minute set up process.