Until round bales arrived on the scene, the major decision when it came to silage systems was whether to go for an open pit or tower silo, with the latter becoming fashionable for a while in the 70s.
That was half a century ago, yet the advantages of the tower have never been fully replicated since.
This was mainly the ability to seal the tower from the atmosphere and so promote anaerobic fermentation, without the need for rolling or the involvement of plastic sheets and film.
They could also be opened easily for second, third or opportune cuts and then resealed without the need to disturb sheeting, which is one large benefit of bale silage. Silage quality was also considered to be superior.
However, they were not without their problems, speed of unloading and loading could be an issue and should the unloading mechanism break down repairs tended to be expensive, especially on the bottom unloading type.
Turning the idea on its head
Having enjoyed a brief moment in the sun, silos faded from the scene over on this side of the Atlantic, yet the idea is not forgotten and one farm in Austria has rekindled the idea, but with a major modification to the concept.
The Hutthaler Model Farm, situated in Upper Austria, is part of a group that grows, processes and sells its produce to supermarket chains and individual shops.
As the name suggests, it is the showpiece of the group and may not experience the same budgetary constraints as other units.
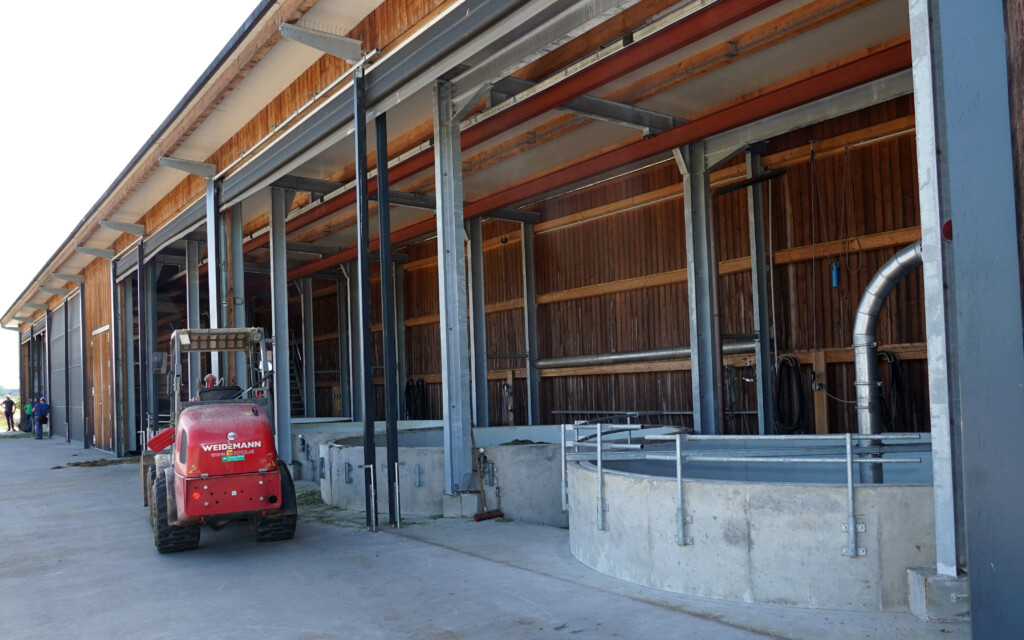
However, it has taken the concept of the tower silos and instead of pointing them into the air, it has buried them in the ground.
The farm has eight vertical silos, each 7m in depth and 3.5m in diameter, giving a total storage volume of 192m3 – equivalent to approximately 250 round bales.
Silo filling
Each circular pit is concrete lined and has drain at the base with lip above the surface of around 0.8 of a metre.
Filling them is a simple task of reversing a forage wagon up to the edge and letting the floor chains feed the silage out of the end of the trailer and into the silo, no loaders or blowers are required.
Crop in the lower part of the silo is compressed by the weight of the grass above it but that at the top needs a little help, and this is provided by the gantry crane which can push down upon it.
It is this gantry crane which is the secret to the whole operation, for not only does it help with compressing the silage, but it is also used to empty the silos in the winter.
It hangs from a frame which runs along tracks suspended from the roof, and is therefore free to run the whole length of the building, taking silage from each silo as required.
The system looks impressive and while Agriland was there, the silos were being topped up with grass being bought in by the Pottinger 5000 Jumbo forage wagon that had been used in the afternoons demonstrations.
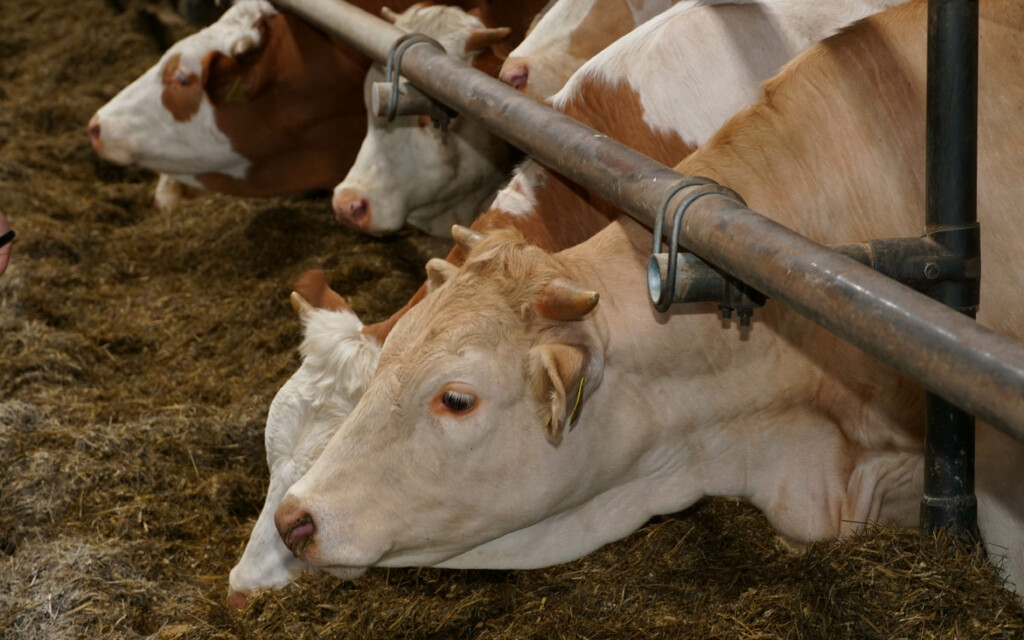
The silage was being used to feed a Charolais cross suckler herd and weanlings housed in a nearby shed which, having ample room to move around in, still sported their horns.
Not for everyone
Although the method appears to be perfectly logical and easy to operate, it might not be suitable for a busy dairy herd.
Filling and emptying the silos is still a slow process compared to modern pit silage and craning out the silage at the base of the tubes will take a good deal longer than using a loading shovel in an open pit.
Building costs are likely to be high, but unfortunately, they were not revealed in the rather brief visit to the installation. There appears to be a lot of work undertaken for a modest capacity.
Leaving 7m deep holes open would be frowned upon here in Ireland, yet over in Austria, people are expected to take greater responsibility for themselves, which may be no bad thing.
It is an interesting concept, but whether it has the potential to gain acceptance in more commercial applications is very much open to question.