The quality of a company’s product emerging from its factory will depend on several factors, and cost is not always the major item.
What is most important, is the desire to make something that will work as it should, and for a long period of time.
Fleming Agri Products Ltd., located in Derry, is hugely conscious of this, which is little surprise given that the company management and many of its staff are from farming backgrounds.
This elevates production from just being a job, to serving their colleagues in agriculture, a distinct difference and one that it believes gives their strong edge in a competitive market.
Functionality is key
Fleming is a company that prides itself in keeping its products simple and robust. Its market is the small to medium-sized farm that appreciates equipment that is functional, without the added cost of the bells and whistles offered by big name players.
However, that does not mean that quality has to suffer, and it takes pains to ensure that everything will hold together over the years.
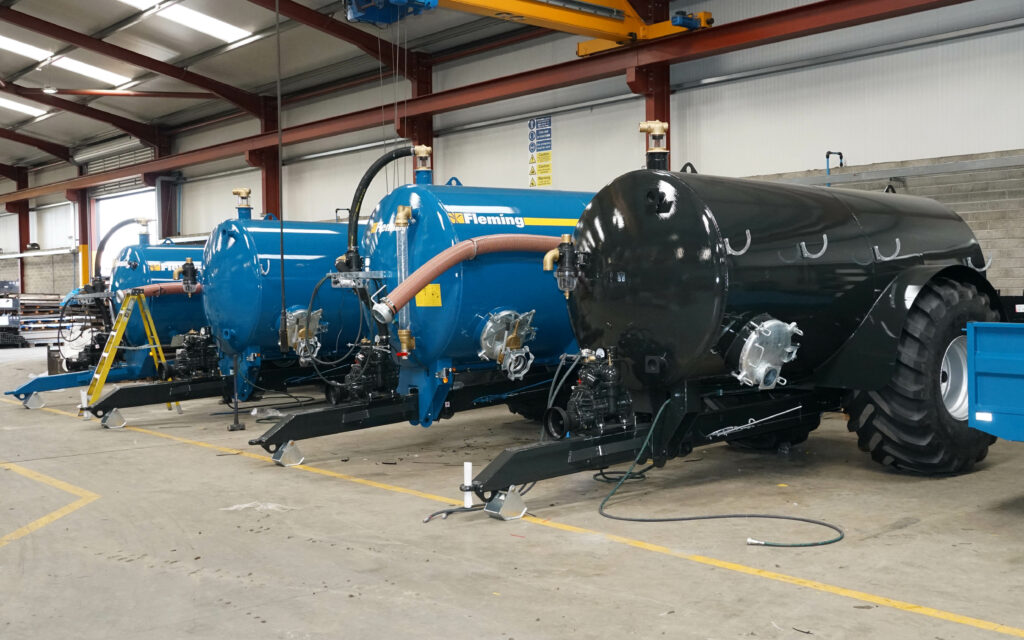
Managing director at Fleming, Jonathon Lecky, makes this point clear when he states that he is not so much interested in how much steel the company uses, but is it the right steel for the job.
With an increasing array of steel grades to choose from, choosing the right material to suit the situation has now become critical, just assuming that mild steel will cater for all tasks is no longer a viable approach.
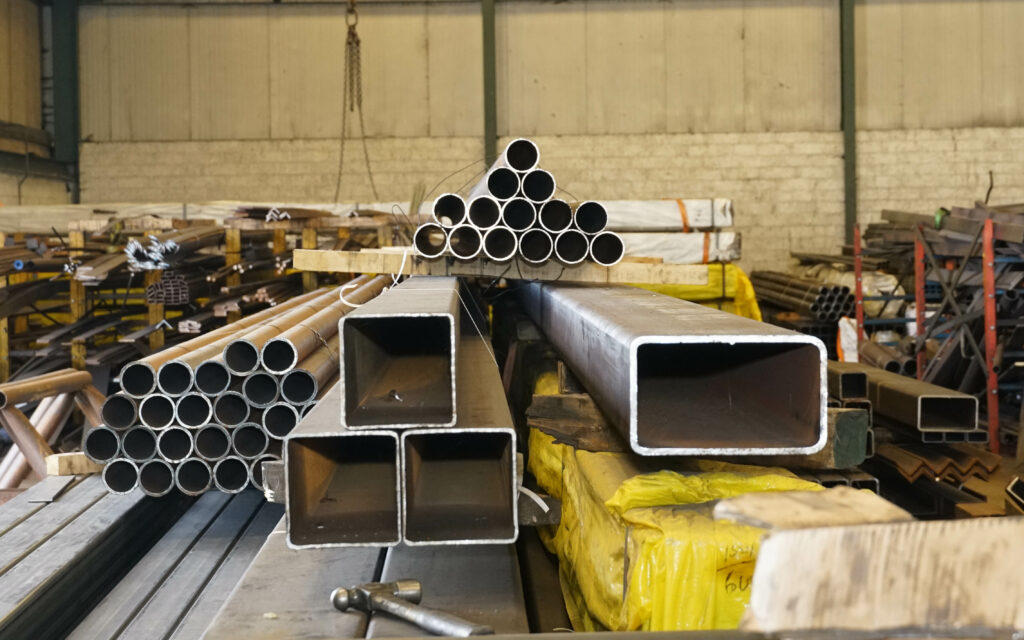
If having the right steel for the job is important, so is assembling it correctly, and to ensure this happens, the cutting and fabrication has to be strictly planned and and those plans implemented.
Filling the market gaps
Yet, before any of this takes place, it has to be decided what is to be built and when, and this relies a lot on the feedback that the company is getting from its dealers and sales mangers as each season progresses.
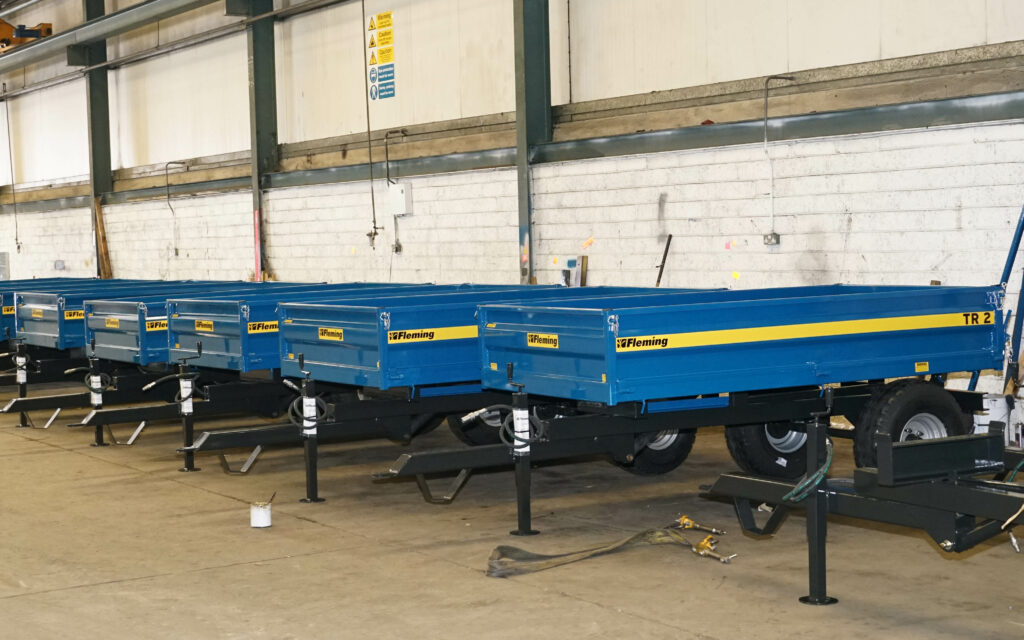
Fleming has become a great advocate for stock control, and not just in its own yard. It keeps tabs on what its dealers hold, and even the approximate number of other manufacturers products out there in supply line.
By doing so, it can gauge what the likely demand for any one product or group of products is likely to be, and plan production to suit, sometimes reducing manufacture to below demand levels, as it is aware of a large quantity of competitors’ products being available.
Factory planning
The manufacturing of machines is done in batches. Once the number of units to be made has been decided, the central computer system will issue a cutting list and it is this that inaugurates the production process.
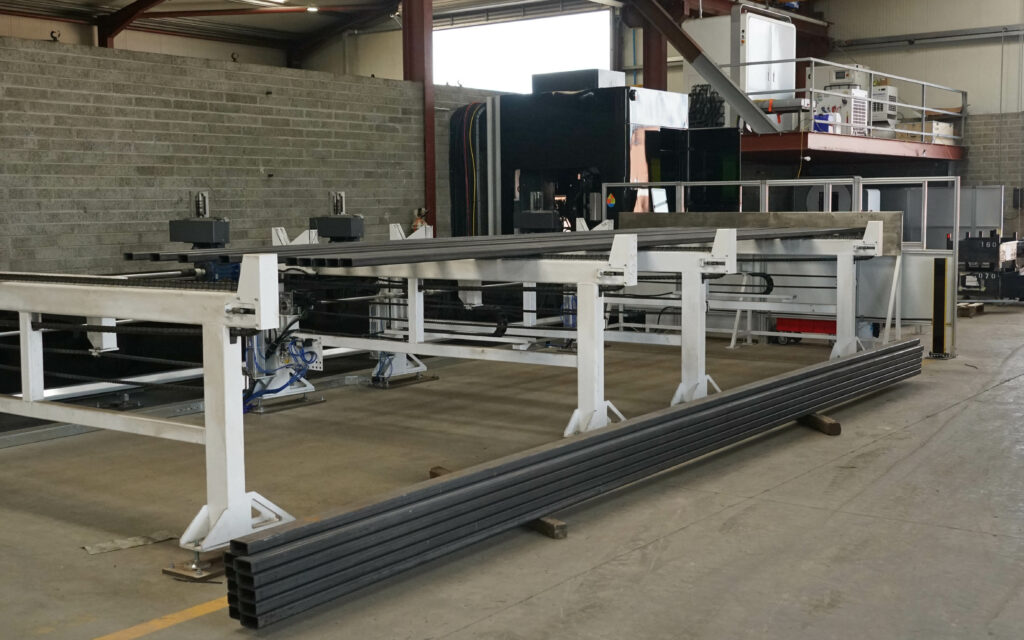
Fleming has recently invested heavily in cutting tools to ensure timeliness and accuracy of the work. Although they have a plasma cutter, laser cutting, for when a finer finish is required, is still outsourced.
One operation that is kept in house is roller forming where the sheet steel is curved into either smaller rollers or larger segments of tankers, thus ensuring the correct material and degree of working is applied.
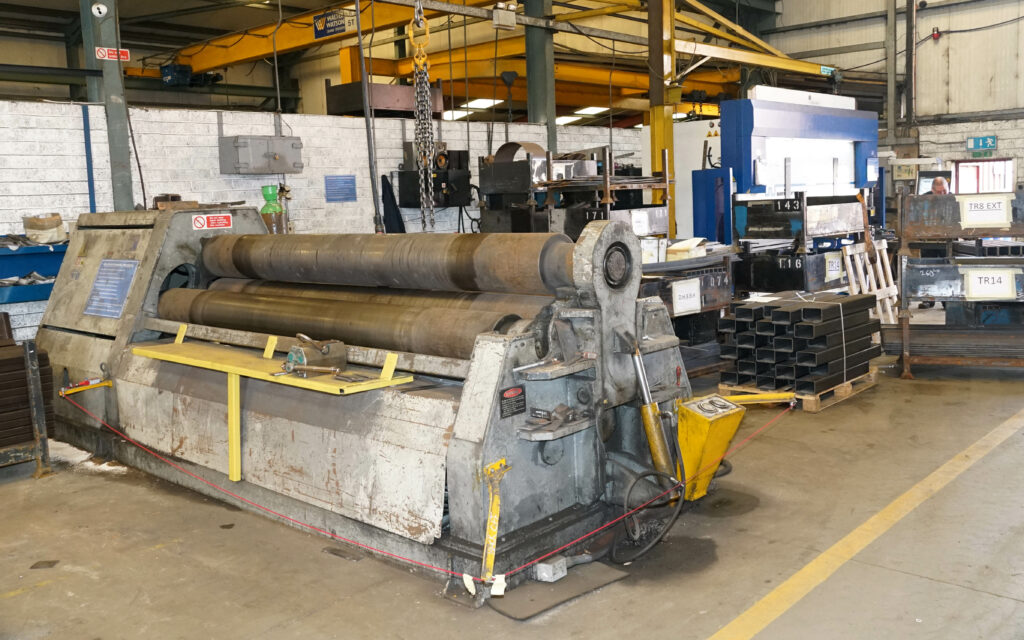
Once cut, the components enter the fabrication and assembly process, which is again directed by the computer, and here there is another notable difference in managing the process.
The staff themselves organise their work, doing whatever job comes up on the system, rather than waiting for instructions from a floor manager.
This approach is said to work better for all concerned, giving each person extra interest in the tasks and a sense of responsibility for the work undertaken.
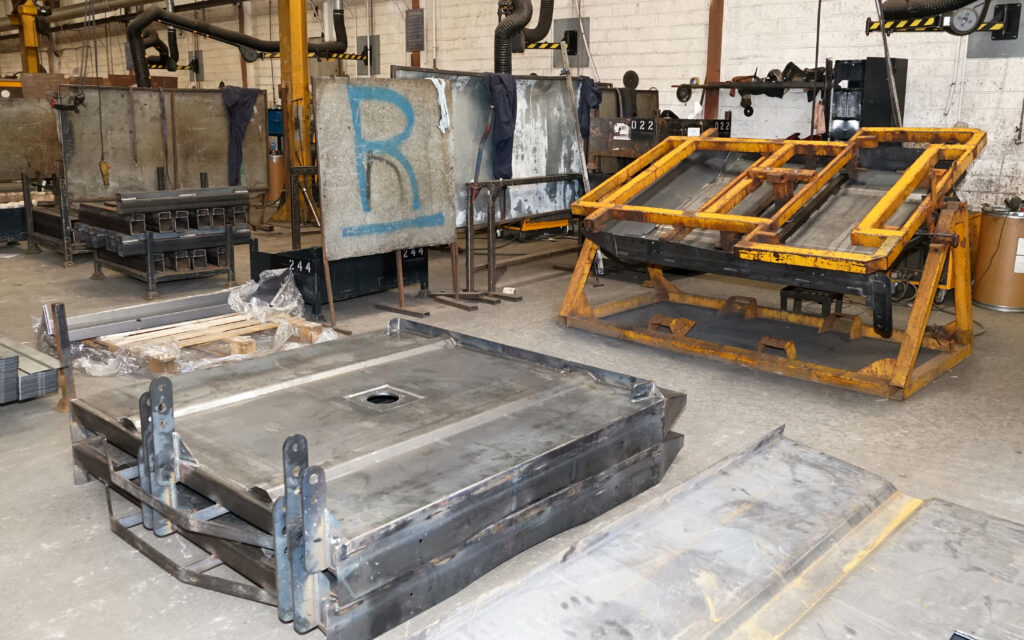
It also offers the company huge flexibility and so contributes to lower manufacturing costs, while still maintaining quality standards.
Staff recruitment and retention is claimed not be a problem, even those with welding skills tend to remain with the company, an impressive achievement given the demand for such personnel in the north, where there is a large number of engineering companies.
Accuracy counts
All of the welding is done with the components securely clamped in jigs to ensure as little distortion as possible – a vital precaution when bearings, shafts and other turning parts rely on the accuracy of alignment.
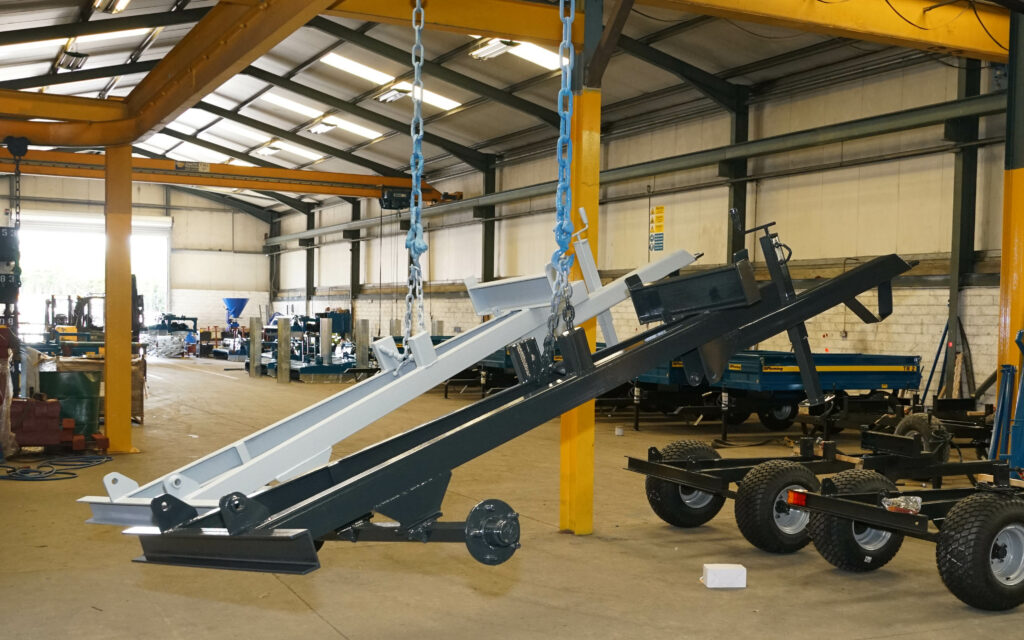
Protection of the steel is left to an etching primer, followed by two pack paint, this is slow baked before the final assembly.
The inside of slurry tankers will also receive a coat of etching primer to give an extended longevity.
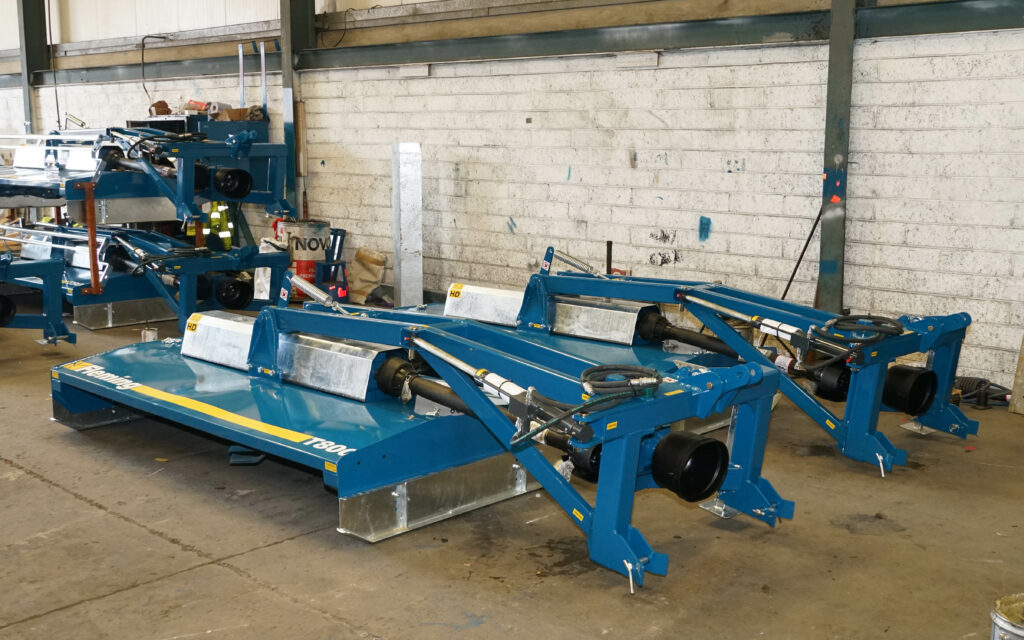
Throughout the whole factory process, there is a good deal of attention to detail. Fleming is not in the game of making large complex machines, so there is not the cost input associated with more sophisticated brands.
Further to its role in planning and recording production, the computer system forms the basis of the company’s spares and parts operation.
When a dealer or customer looking for a part logs in to view a product, they are seeing exactly the same drawings as the factory uses to produce the machinery.
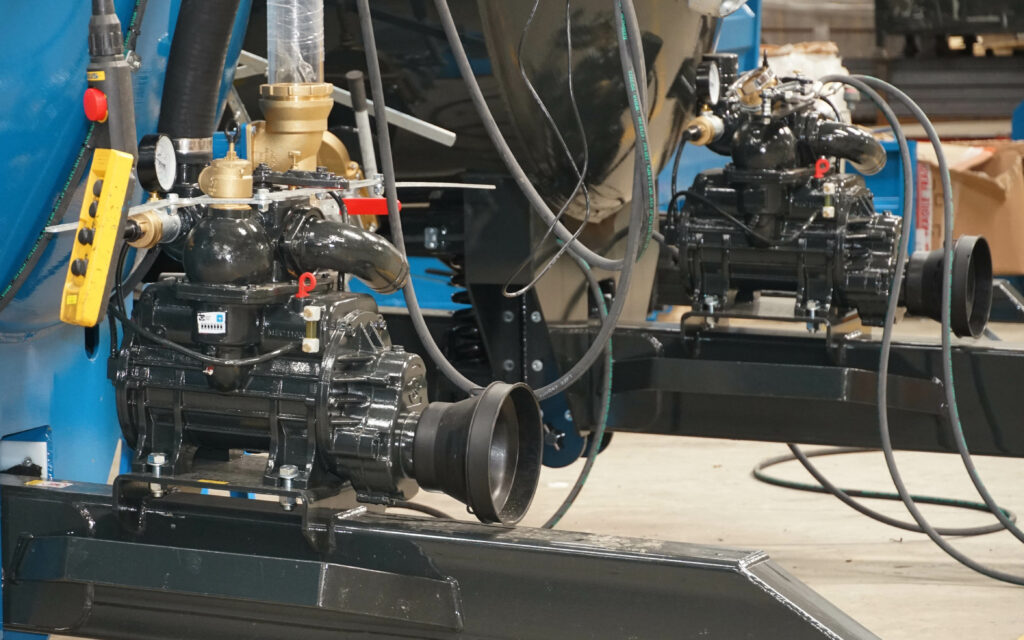
By utilising the same database, Fleming claims that part identification is a lot quicker and more accurate, allowing customers to get the machine back to work in the quickest possible time.
Fleming is keeping its factory busy despite acknowledging the sales downturn this spring.
The company is confident that farmers will start buying again and feels that as a provider of simple, budget friendly equipment it will be well placed as farmers start buying again.