The company has now given the whole range its first major revision, with the emphasis on making the balers more attractive to larger users and contractors.
The improvements are also in line with Pottinger's stated strategy of treating silage-making as a linear process rather than a series of disparate operations, that may be addressed with an array of equipment from different manufacturers.The new models
To help bring some clarity to the various models available, all those that have 'F' after their number are fixed chamber, while those with a 'V' are variable. When a 'C' is added it means that it is a combination model, i.e. one with a wrapper. Altogether there are now 12 models on offer. Starting at two basic fixed-chamber models and rising to the Impress 3190 VC Pro variable chamber which can produce bales up to up to 1.85m in width, although only bales with a diameter of up to 1.5m can be wrapped.A tighter squeeze
Perhaps the most basic change is the increase of baling pressure by 20% across the board. This extra compaction will reduce oxygen inclusion as well as ensuring the bales retain a better shape, for loading and stacking.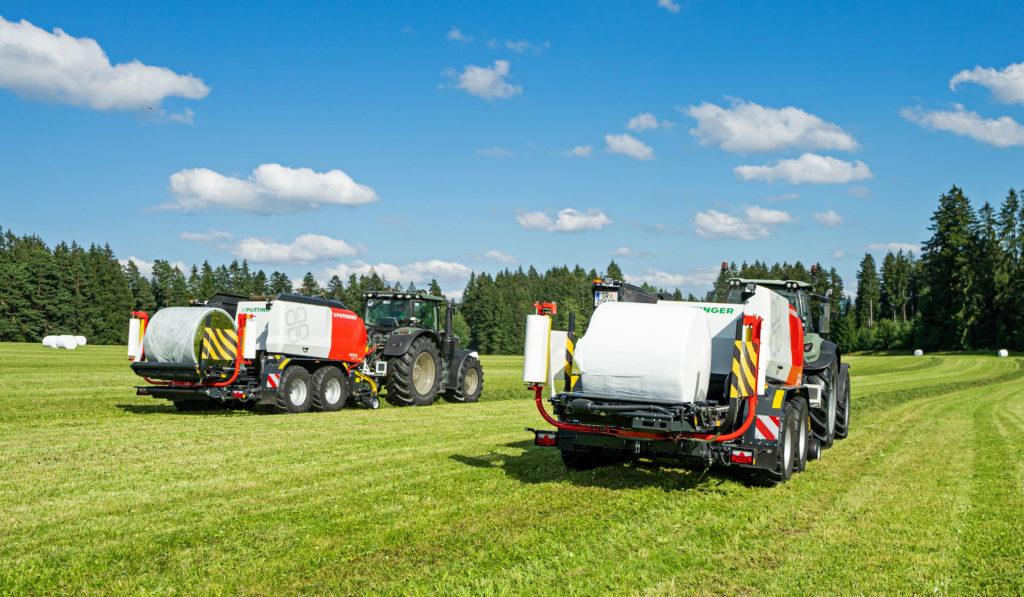
The new binding unit is installed on all models and switching between net and film has been simplified - there is now no need to remove the roll of one when wishing to change to the other.
Changes to the wrapper platform enable it to rotate the bale before and after the wrapping process. This tidies up the ends of the binding and wrapping layers, putting an end to ribbons of film dangling from the bales.Pottinger banishes darkness
There is an optional LED lighting package for all Pro models to illuminate the major areas of activity. These include the pick-up, bale ejector and wrapper platform.LED strips with switches are also installed under the side panels for maintenance work and changing rolls of film.
An optional hose reel with air supplied from the air brake system through an overflow valve, is available to help clear dust and debris from the machine's mechanisms. Moisture sensors are also offered as an extra with the results showing on the in-cab display. The baler's monitoring system can be supplemented by an optional camera system with a screen displaying four separate images.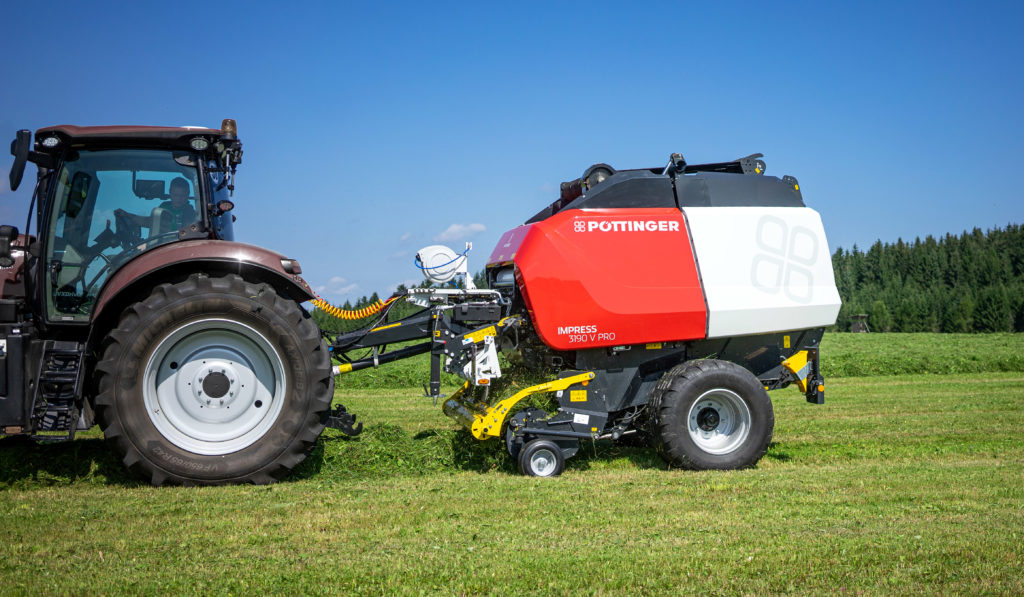