Tractor Guidance systems has, up until now, been mainly based on satellite networks such as GPS or Galileo, however, New Holland has just won an award for a LiDAR or vision-based system for use on speciality tractors.
The advanced guidance system developed for New Holland T4 FNV specialty tractors has won a Technical Innovation award in the scheme run in advance of November’s EIMA International farm machinery exhibition.
The company notes that it was developed to help address the lack of skilled operators faced by many specialty crop producers, and ease the workloads of such growers and their staff.
Overcoming satellite blind spots
Advanced Vision Assisted Guidance is LiDAR-based, and manages steering movements both in the rows and at row ends, in addition to rear implement control.
As a result, it is said to be effective in situations where satellite-based systems are not, bringing benefits which include increased safety and comfort from reduced operator fatigue.
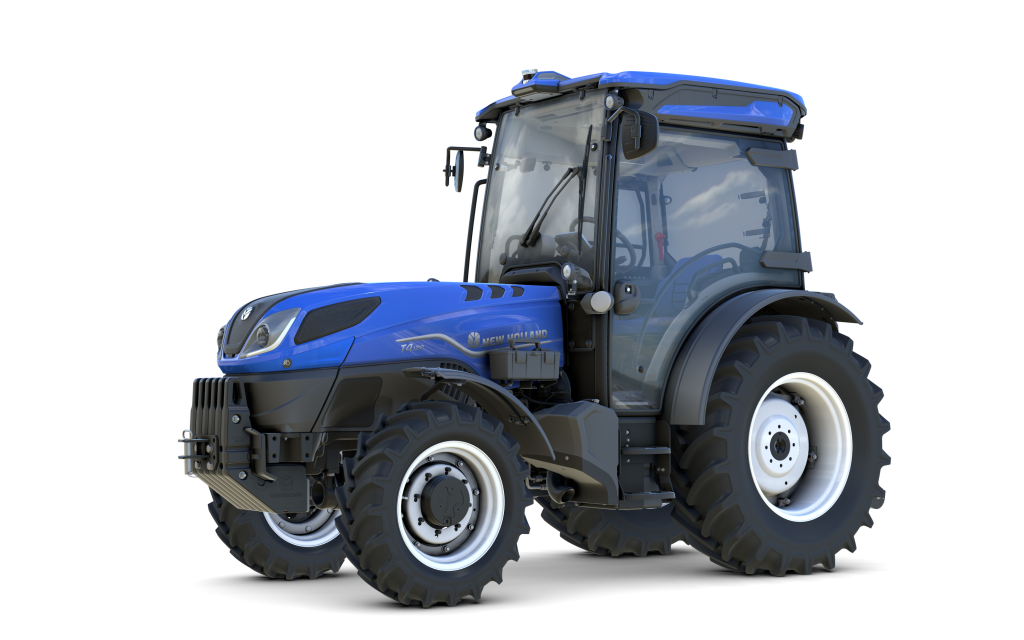
New Holland claims that the technology has the potential to help retain experienced operators by relieving them of repetitive and arduous tasks, while also providing significant support to those less skilled.
Greater precision also means reduced environmental risk and enhanced performance through optimising use of fertilisers and crop protection products based on real orchard or vineyard field conditions.
The system is based purely on LiDAR sensor technology, using simultaneous localisation and mapping algorithms, and thanks to the elimination of the satellite element there is no risk of errors and incidents resulting from any loss of GPS signal.
New Holland ensures safety
It is also able to recognise row ends and incorporates a path planner to perform headland turns, with different path shapes available.
A collision check mechanism means that if the headland does not have the required characteristics, the system will advise the operator, avoiding possible collisions with trees/plants or other objects.
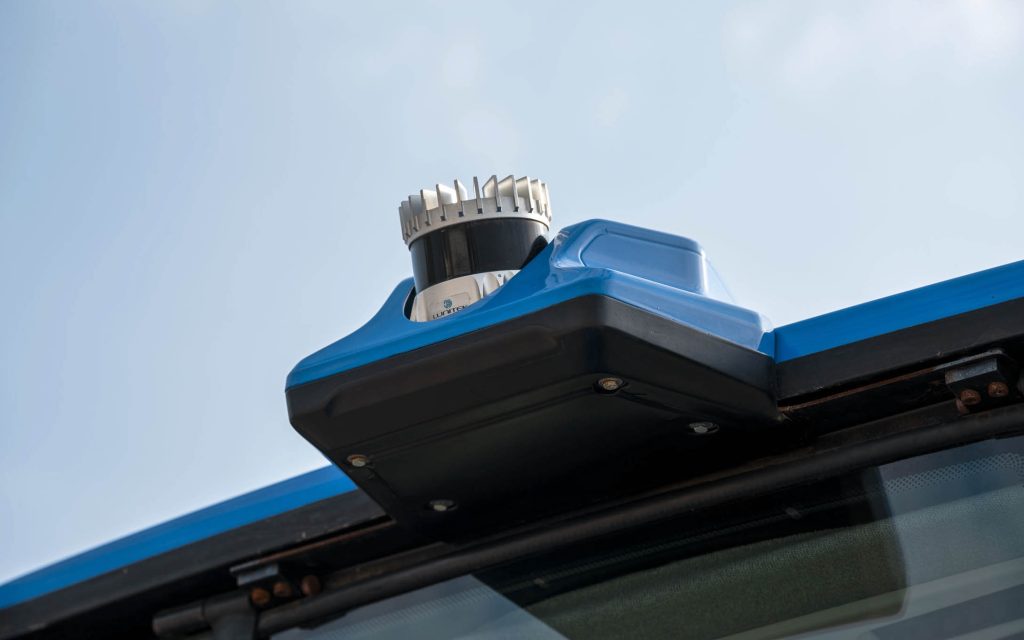
Advanced Vision Assisted Guidance integrates the use of perception based implement control, allowing automation of various tasks for different implements.
With a trailed sprayer connected via ISOBUS, e.g., it can be used to automate left and right section control at row-ends, or account for any missing tree/plant in the row.