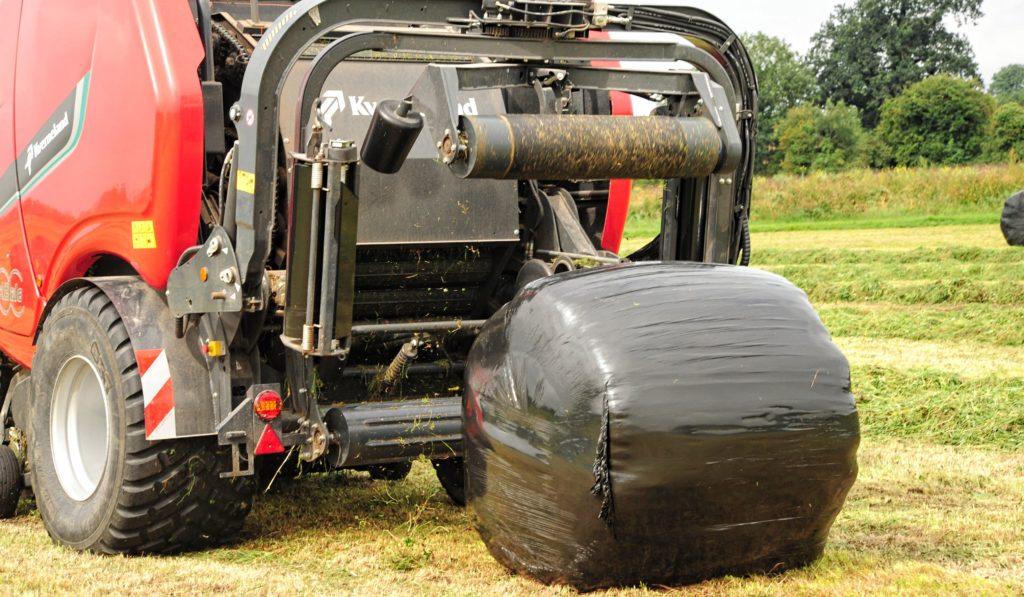
The challenge of a round baler
https://youtu.be/_8NnChZNswo Watch the baler in action in the video above. Unlike square balers, which have a linear form of action, round balers require an interruption in the constant flow of material to secure and eject the completed bale. In a round baler there are up to four distinct phases of operation. The first is the collection of the grass and its chopping, the second is the formation of the bale itself, while the third is the tying and ejection.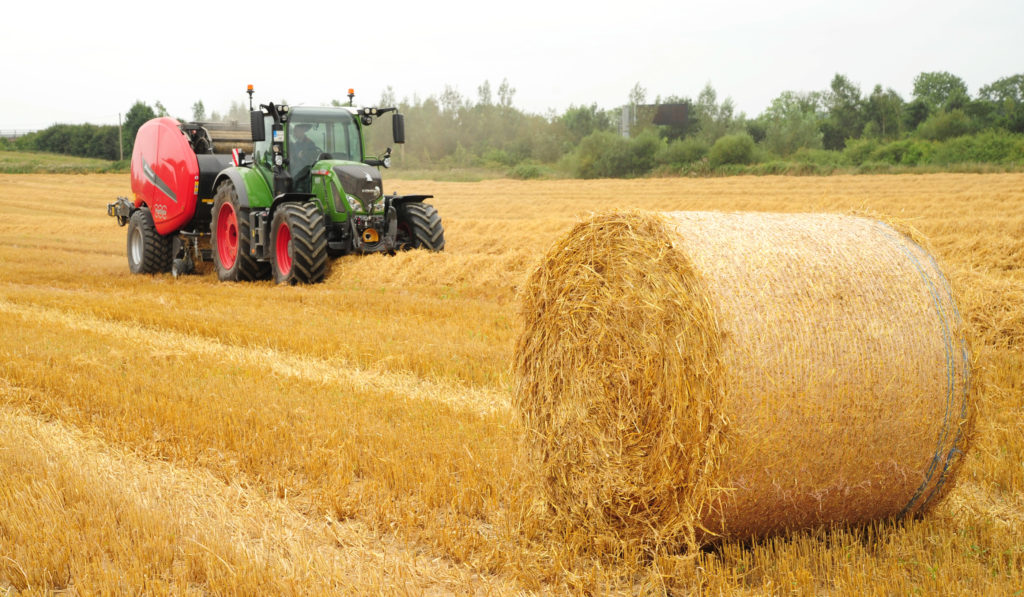
To achieve continuous flow, the problem that has to be overcome in a round baler, is the need to halt the flow of material into the chamber while the completed bale is being tied.
Despite the concept of circular bales being around since at least 1910, this has been a problem that had not been successfully addressed until recent years.Kverneland's solution
Kverneland believes it has now perfected the answer and, what's more, it's one that appears to work well in the field, offering an average increase in productivity of up to 25%. The solution, on paper at least, is quite simple. Instead of the tractor stopping while the bale is being tied, and so halting the flow of material, it continues to travel down the swathe picking it up as it goes.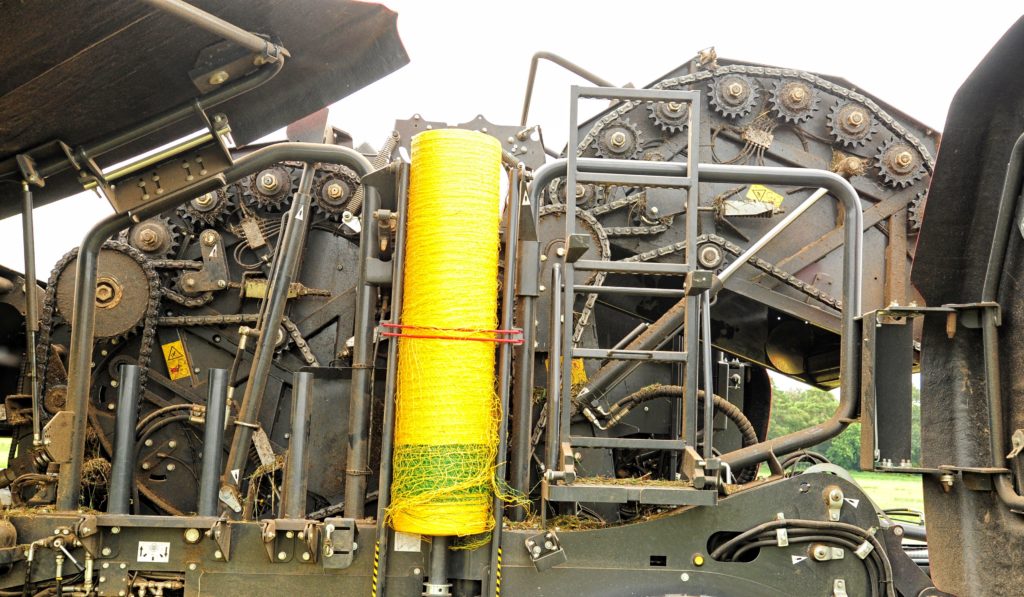
Rather confusingly it is referred to as the secondary chamber, although it actually sits in front of the main primary, chamber.
This secondary chamber is, in effect, a half-sized baler which produces a small bale itself. This proto-bale is then passed back into the main chamber, when that has completed tying and ejecting the larger, finished bale.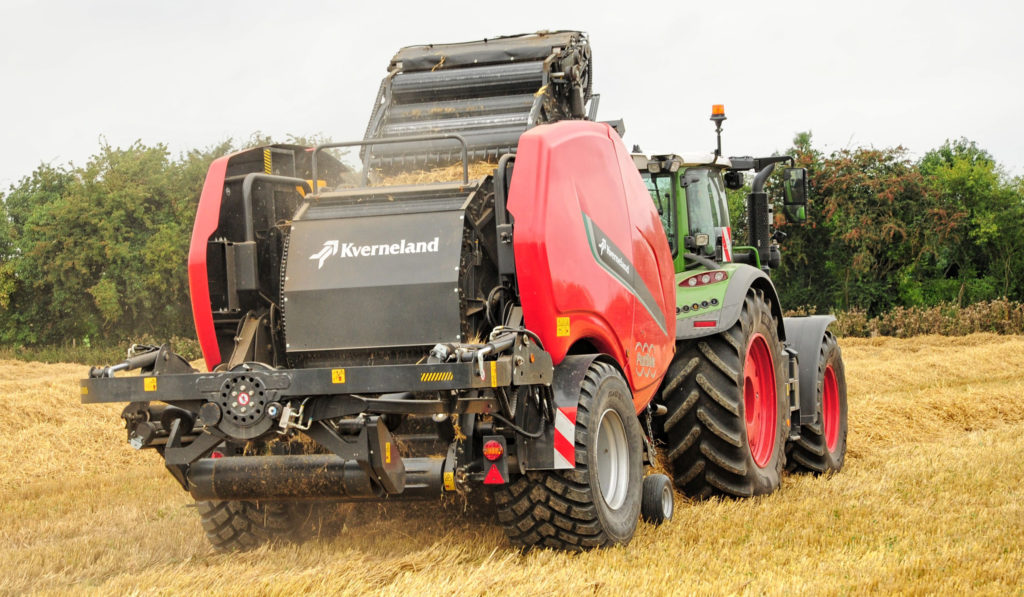
Other advantages of the baler
The foremost benefit of not having to stop is the time saved over standard balers; there are are two other major benefits to the method. The first is fuel efficiency. Stopping and starting a combination of tractor and implement that can weight up to 10t is expensive on diesel. It can also increase wear and tear on both machine and operator.
Kverneland FastBale
Kverneland has had many years of experience producing round balers and its products are already well-known and respected in the market. The FastBale machine reflects this with an apparent sturdiness that suggests it will be capable of hard work over many seasons. The wrapping unit is a case in point. When empty, it is carried close to the ground to enable a complete bale to roll down into it. It is then raised so that the wrapping arms have room to pass underneath.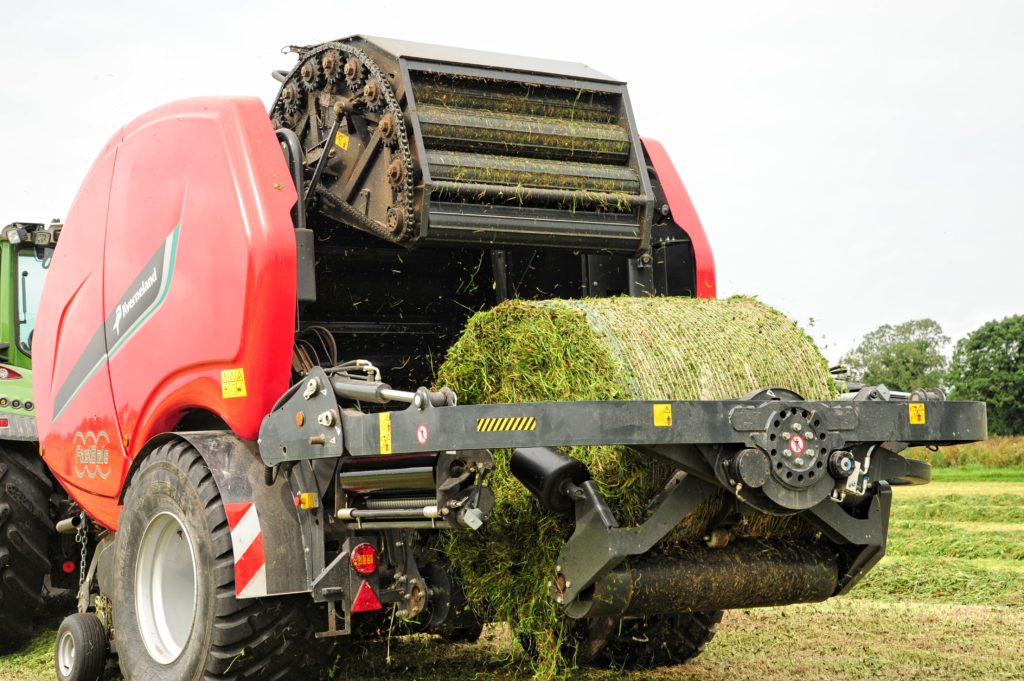
Baler essentials
The pick-up has a cam mechanism either end to prolong longevity and has a central support mechanism to further extend bearing life. Net or film can be applied in the main chamber, with only a slight difference in routing the two required to change from one to the other.All up weight is just over 7,500kg with flotation tyres being available, as shown here, for softer conditions.
The baler is fully ISOBUS compatible and the tractor's own screen can be used to monitor and adjust the baling operation. There are three cameras strategically placed to allow the baling operation to be viewed. Future developments will include weighing of each individual bale to give an an average on total per field. Moisture analysis is also likely to become available at some point.