With the dramatic increase in fertiliser costs, the spotlight has been turned on its efficient use like never before, and with that has come the realisation that despite great advances in digital technology, it is still something of a ‘hit and miss’ affair.
Applying fertiliser via a liquid medium is not a new idea, spreading urea in this fashion was something of a fashion back in the 1980s, however, ready prepared compounds are now available and the battle for market share is heating up.
Liquid or granular?
According to the advocates of the latest liquid products, granular fertiliser has three main drawbacks, which liquid fertilisers overcome.
The first two concern the accurate placement of the nutrients.
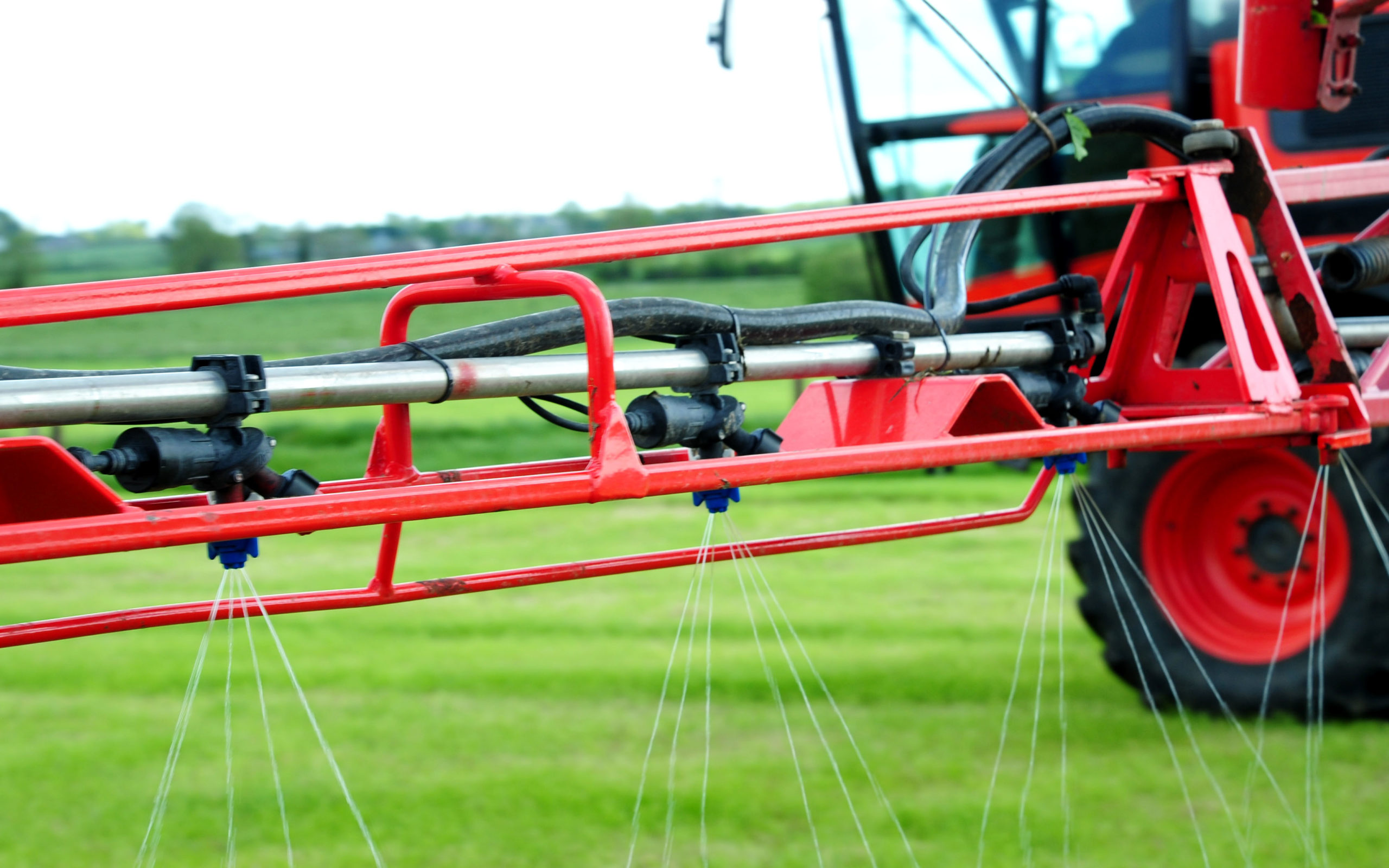
Spinning disc spreaders cannot, unfortunately, provide a clean cut off line for the product. Granules do not just drop vertically to the floor once they have reached the maximum desired distance.
This ensures that either the hedgerows get well fed or that the edge of the headlands get a lower rate as the tractor drives further from the field margin.
Nitrogen where it is needed
A sprayer will place the nutrients exactly where they are required. The nozzles are placed 0.5m apart, as is standard, and the product will land within a few centimetres of the boom tip, eliminating the headland conundrum.
The second problem with placement is that granular fertiliser does not cover all the ground, it only dots the surface.
The lighter the application rate, the more acute the problem, as the greater the gap between the various pellets, the less even the distribution.
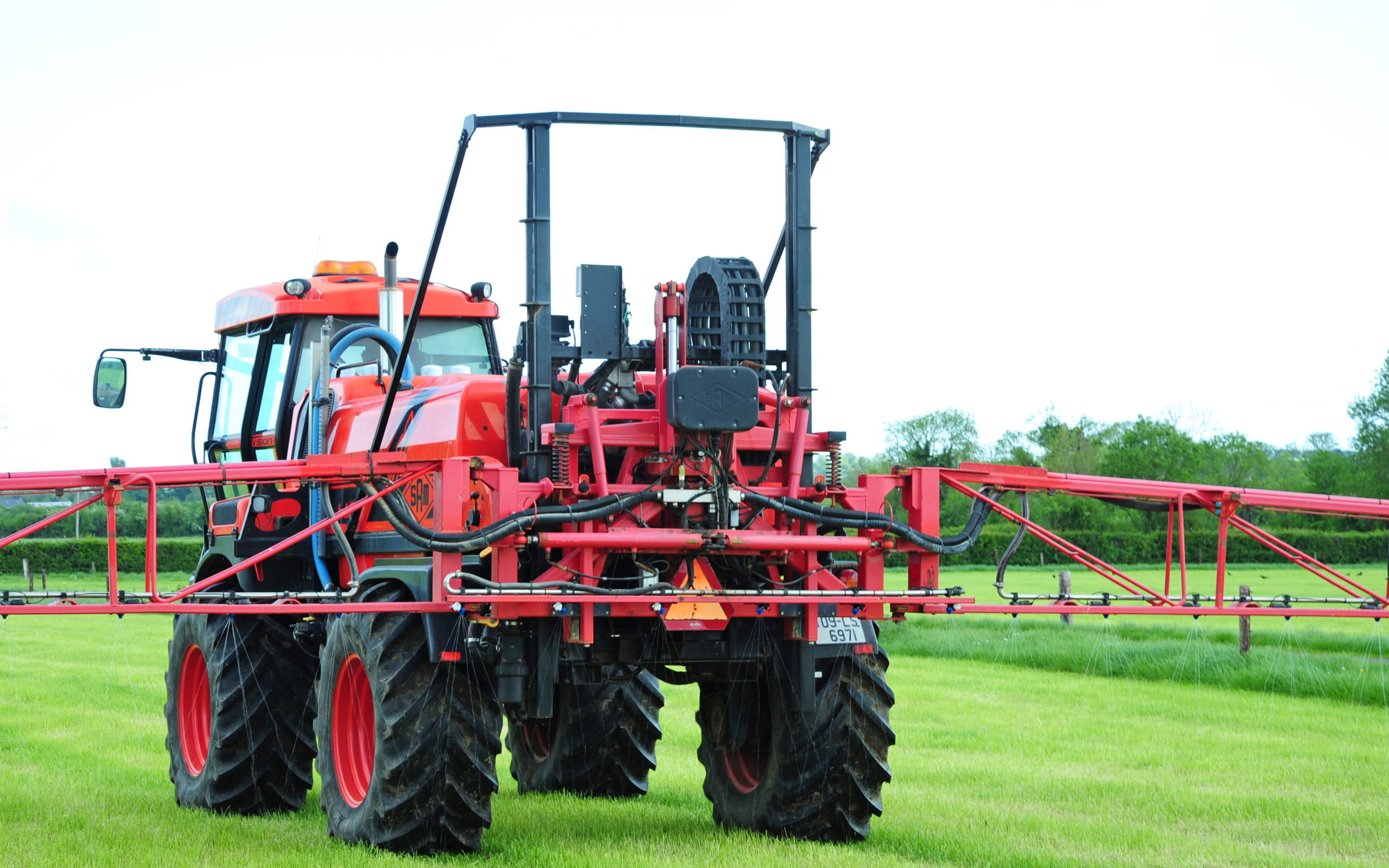
Allied to this issue is that the various pellets within a compound will have different flight characteristics and these will not be constant between brands, or even within the same brand over time.
The upshot is that despite great care being taken in getting the application rate correct, the very nature of the material mitigates against truly accurate distribution of the three major elements concerned.
Volatility of nitrogen
The third major concern is that granular fertiliser lies around on the soil surface until it is washed in by rainfall.

This may not be a problem as far as phosphate and potash are concerned, but nitrogen fertilisers are volatile and a good deal of it may evaporate before it enters the root zone.
Liquid fertilisers overcome this by already being in solution and so enter the soil just as soon as contact is made.
Liquid application accelerates response
Herein lies the key to the success of liquid fertilisers according to its backers.
The overriding objective of applying liquid fertilisers is to target the soil and not the leaf, this is in complete contrast to spraying pesticides where the aim is to achieve a thin film of active ingredient across the leaf surface.
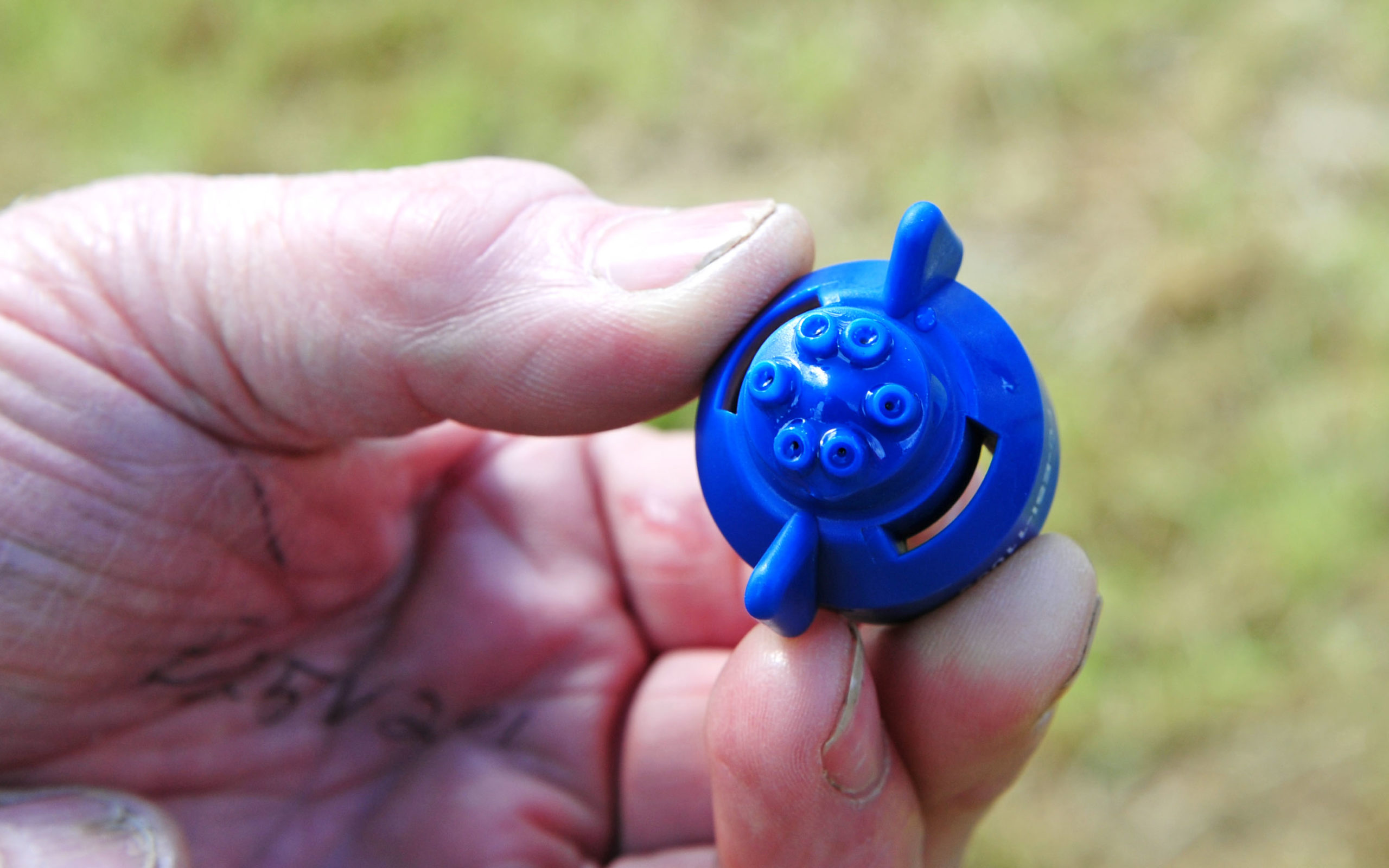
To do so does not usually entail any special adaption to a modern sprayer other than the fitting of high volume nozzles that produce a series of jets which penetrate the canopy, rather than a mist to coat it.
Contractors’ choice
One contractor who is in his second year of offering liquid fertiliser application is Seamus Lanergan of Holycross, Co. Tipperary.
Seamus had been busy spreading fertiliser for the local co-op when he was approached by Brian Reidy, the area representative for Omex Liquid Fertilisers, who suggested that he try the liquid approach instead.
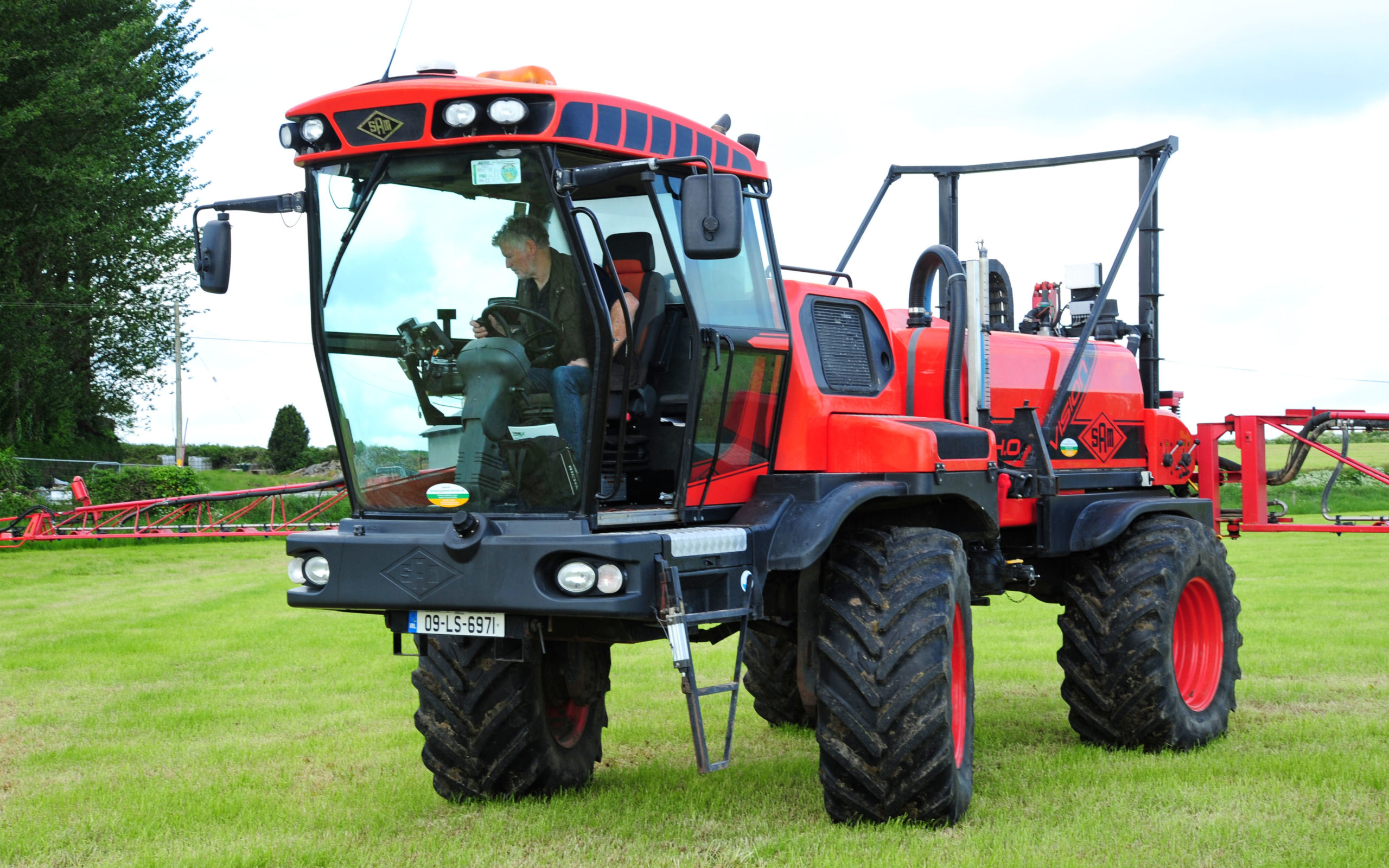
With the decision to convert to liquid application came the purchase of a second-hand SAM self propelled sprayer which, even at 13 years old, is still in fine fettle and perfect for the job.
Powered by a 200hp Deutz engine and running on low ground pressure tyres, the fully hydrostatic machine offers a comfortable ride, convenience and, above all else, the ability to cope with a rapidly increasing workload.
Expanding demand for liquid application
The liquid method has really taken off this season according to Brian and Seamus, and although Seamus has yet to breach the 1,000ac/week mark, he feels that next year will see it happen on a regular basis.
While there is great merit in applying fertiliser via a liquid medium, there is still the need to apply the solution accurately and to enable this, the sprayer is fitted with a control system based on a RDS (now Topcon) platform.
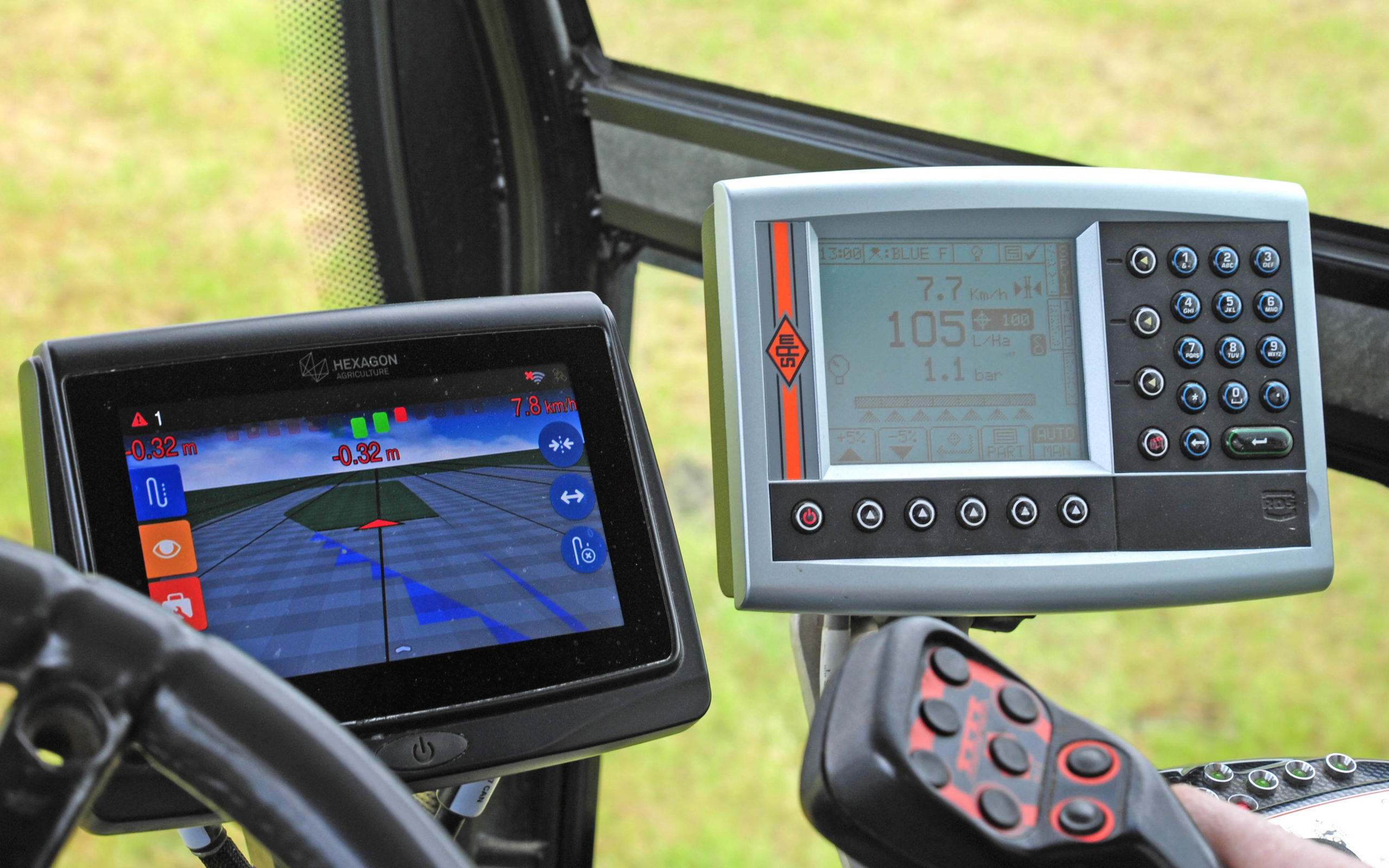
This is coupled to a GPS system by which the field is navigated, creating lay lines for the operator to follow. Presently there is no autosteer but that may come with an increasing workload.
The 24m boom is divided into seven sections across its width, with compressed air being used to operate the nozzle valves, giving a positive opening and shutting off of the flow.
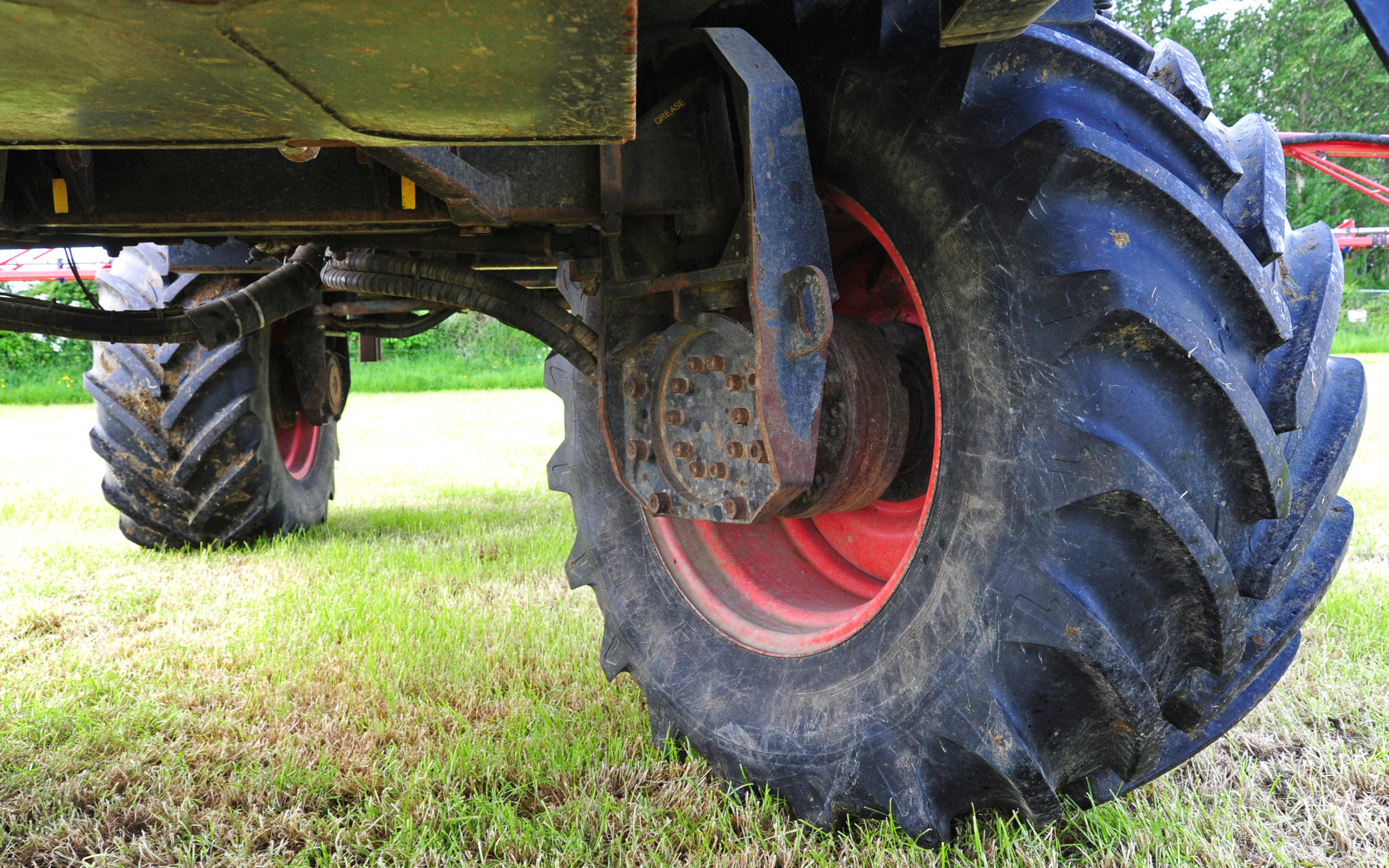
Indeed, all the electrical components are kept as well away from the spray as is feasible, with electric over air being the preferred method of control wherever possible.
This adds greatly to the reliability and serviceability of the machines, for problems can usually be located by listening for the hiss of air escaping rather than trying to trace faults with a multimeter.
Digital control
In the field, the desired application rate is set on the SAM (RDS) screen and the flow to the booms is altered according to the speed, within a certain window.
Normal forward speed is around 8km/h and the system can happily cope with a 50% deviation from this. Beyond that, it will start to struggle and new parameters may need to be set on the control screen.
Section control is an important part of the set up; this can be overridden if required but as a rule it performs well and the GPS screen showed it working neatly with a minimum of overlap, and nothing missed.
Farmers perspective
The machine was seen working Conor Ryan’s farm in Co. Tipperary, a regular customer and neighbour of Seamus.
Conor runs a 200-head dairy herd and has become an enthusiastic convert to liquid fertilisers over the past two seasons.
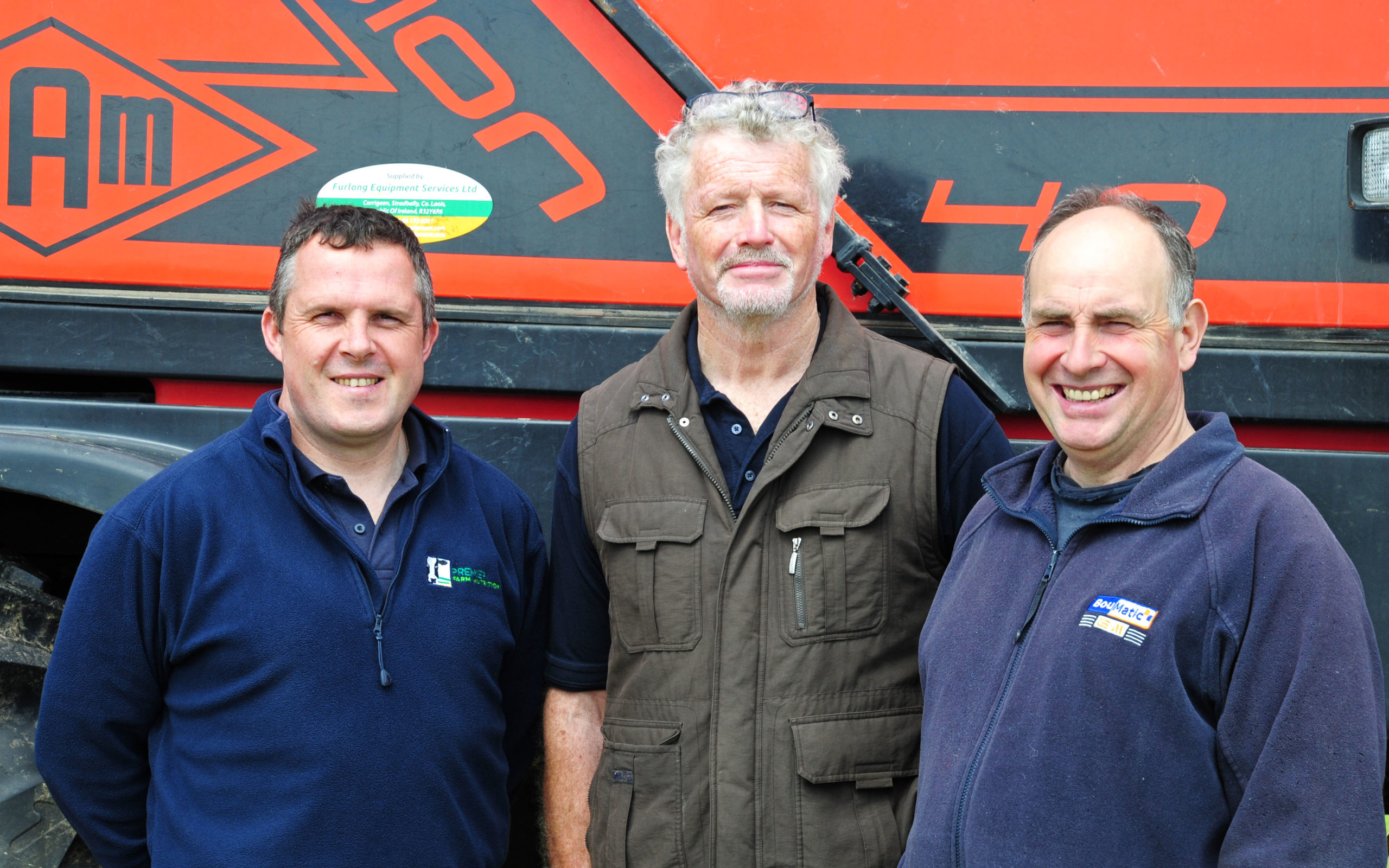
There are many reasons for switching, one of the primary motivations being the greater efficiency of nitrogen use.
Conor is cautious about putting actual numbers to the saving himself as it is still early days. Brian Reidy, however, suggests that the same growth can be achieved with 160 units of liquid N as opposed to 200 units of granular fertiliser.

This saving compensates for the extra cost, yet Conor notes that there are many other significant benefits, including a quicker response, leafier grass, denser sward and healthier cows with an excellent conception rate so far this year.
He is also far happier to be able to dress the field up the margins at full rate, making full use of the headlands without wasting N on non-productive areas.
Altogether he is delighted with new method and finds that many other smaller advantages become apparent as he becomes used to it over time. He won’t be moving back to granules anytime soon.