Hot on the heels of its sister company offering a premium tractor kitted out for digital farming, Fendt has been showing off its latest Vario 700 models built around the new AGCO CORE 75 engines.
These latest machines are completely new to the Fendt line-up, although sharing similar power ratings with existing models, a state of confusion which should ease over time as the older ones are phased out.
All new tractors
To help matters, the new tractors are also labelled Generation 7 and they slot in at the top of the segment with the power availability stretching from 203hp to 303hp.
The new engine is AGCO’s latest CORE75 which is designed to be adaptable to multiple fuels and meet stage five emissions standards from the ground up.
So far Fendt is the only brand under the AGCO umbrella to utilise this engine; we will not be seeing it in Valtras until the Finnish company’s sixth generation of tractors is launched, which is likely to be in 2025.
Fendt has taken a novel approach to engine boost, rather than the engine respond to demand from the power take-off (PTO), it increases its output by up to 20hp to compensate for secondary power drains, such as air conditioning and the alternator.
Low revs and fewer parts
Throughout the design process, the overriding concern was to keep the engine revs as low as possible and reduce the number of components.
Peak torque is held from 1,150rpm to 1,500rpm with maximum power becoming available at this higher figure. It is not an engine for revving hard and its less hurried soundtrack takes a little getting used to.
Fendt claims an overall 15% reduction in fuel use over a variety of tasks in relation to the last engine of this power rating, due to this philosophy and other modifications.
Keeping it cool
One of the more notable of those modifications is the novel approach to the design of the cooling package which, we are told, can save up to 1.3L/hour compared with the traditional arrangement.
The main change is that fan is situated at the front of the cooling pack and so pushes air into the radiator matrix, rather than trying to pull it through.
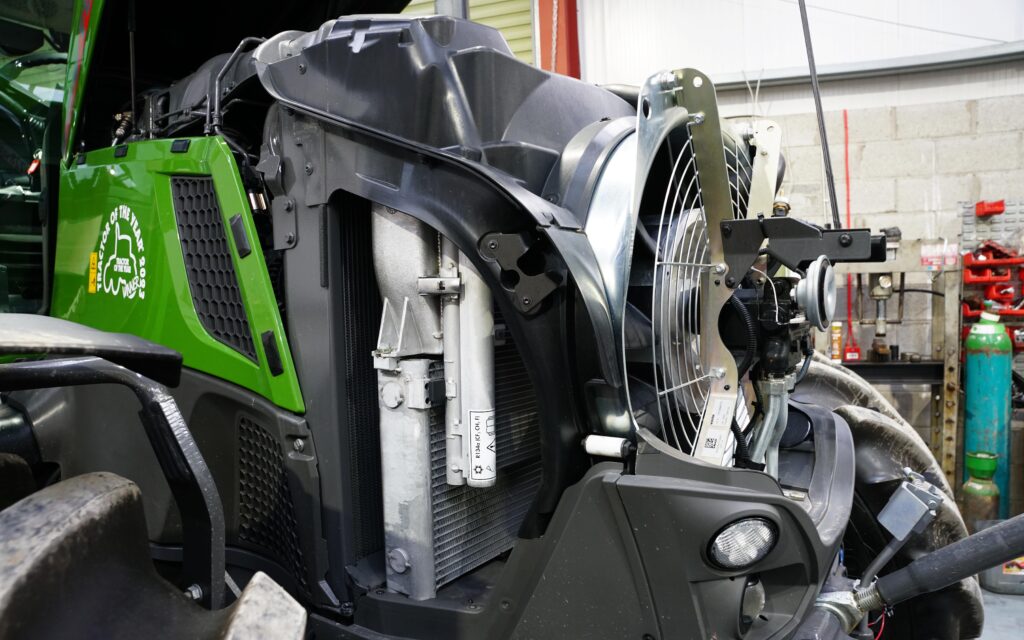
Applying a positive pressure to the front of the radiators ensures a denser flow of air, as opposed to a fan drawing it, which relies on a drop in pressure to cause movement, resulting in a smaller mass passing through.
The greater the quantity of air that travels through, the more heat will be carried away, which is then vented out of the side of the bonnet in this latest 700 model, rather than have it flow over the engine.
Further attention to detail is found in the main cooling fan which has a very fine tolerance between the blade tips and the shroud, reducing turbulence and increasing its efficiency.
This is possible due to the radiator assembly being mounted independently of the engine, isolating it from the vibrations that would otherwise dictate a greater clearance.
Twinned transmission
The Vario 700 7th Generation series has inherited its transmission from further up the Fendt lineage. The CVT is not new, it has been in the 1000 series for several years now, so it can be counted as well tried and trusted in tractors of 500hp+.
Known as the TA190 it differs considerably from the standard CVT in that there are two internal pumps, one for each axle.
This arrangement is a little more complex and expensive than the normal version, however, it does have two great advantages.
The first is that each axle is powered individually, allowing a tighter turning circle, while the second, is that the system automatically applies power to wherever there is the most grip.
It is, in effect, two transmissions condensed into one, and the system is probably unique in that rear and front axles share the same engine but different transmissions that operate independently of each other.
Another feature of the TA190 is that there is just the one range to cope with field and road operations, whereas the standard type has an A and B range to cover these two situations.
All new front axle
During development of the latest Vario 700 series, the transmission proved to be so effective that it ripped apart the standard front axle.
The company faced a choice, it could have have abandoned the idea of fitting the transmission, or it could spend more money on designing a new front axle.
The latter was chosen and it is because of this focus on engineering solutions that Fendt holds a premium price in the market.
The front axle of a turning vehicle always travels slightly further than the rear, this difference can be accommodated by the latest transmission which eases stress on the front drive train, reduces tyre wear, eliminates soil damage through scrubbing and is altogether more efficient.
With the tighter turning circle comes greater potential for the use of a fron- end loader, and here Fendt has designed a front-end loader that is suited to the size and shape of the tractor, it will only fit the Vario 700 series.
Contamination free cab
The cab is said to be the only component carried over from the 6th Generation 700 series, but it has not gone without some adaption and modernisation.
It is now possible to fit a category four filtration system for crop spraying, and positively pressurise the cab to ensure vapours cannot enter through door and window seals.
The filter may then be easily removed for other operations to save it from clogging.
Central Tyre Inflation (CTIS) is not a standard feature on Fendt tractors. However, where it is offered as an option, it is enthusiastically taken up, 85-90% of UK farmers will tick the box when ordering.
Yet this still leaves the question as to what tyre pressures should be set at. A calculation which, Fendt believes, should be left to the tyre companies with recommendations for field and road use.
Yet, there are so many variables involved it is difficult for any definitive answer to be provided, thus it will come down to general guidance and experience.
However, with the ability to control tyre pressures from the cab, there is at least the option of regular and convenient adjustment.
Full production of the new Vario 700 models will start after the summer refit of the factory with the first deliveries of pre-ordered machines in the autumn.