Cutting silage by a self-propelled harvester is now such a standard feature of the season that most of the drivers working alongside them will have been born well after they appeared on the scene during the 1980s and 90s.
Dragging a harvester along behind a tractor must seem as archaic as the scythe to many, although it is a method that fits in with a few farming enterprises and there is still a small demand for the machines.
Horsepower matters
Going self-propelled makes a lot of sense. Output is purely dependent on power and even the biggest tractors pale in comparison with harvesters developing well over 1,000hp.
When dealing with this sort of energy input into the chopping mechanism, standard PTO shafts are just not up to the task.
It is not just the transmission of that power but also the mounting of a heavy cylinder revolving at high speeds which requires a degree of strength, rigidity and stability that can only be provided in a specialist machine.
It has taken around 50 years to get to where we are today.
Machinery manufacturers never stand still for fear of becoming extinct, and so a lot of development work had already gone into creating bigger and better trailed machines, but these were limited to whatever the tractor could supply at the PTO.
There were efforts made to overcome the lack of tractor power without going to the expense of a self-propelled unit by mounting an engine on the harvester to power the chopper directly, leaving the tractor to do the hauling.
This was certainly an improvement, but it could result in a tractor, a heavy harvester and a full trailer of silage relying on just one set of brakes, not an ideal situation on slopes, especially if wet.
Mixing and matching
Self-propelled was the way to go and both New Holland and Claas went down the route of attaching a 100hp+ engine and drive axle to an existing chopping mechanism and pick-up reel.
Claas entered the fray in 1972 with the Jaguar 60 SF which took the header and mechanism from the Jaguar 60 trailed model and mounted it on a combine chassis, possibly the Dominator 80 as this had the 120hp engine which featured in the new machine.
John Deere was more ambitious with its 160hp 5200 and 212hp 5400 models announced in 1972. These would have been high performance machines at the time and contractors on this side of the pond may have felt that they didn’t have the tractors to keep up with them.
New Holland brought out its 1880 at roughly the same time, which also combined the elements of trailed chopper and combine drive axle, yet both European companies had been beaten to it by a Field Queen, a company that had been making self-propelled forage harvesters since 1950.
Field Queen leads the way
Given this head start, it is of little surprise that by the early 1970s this American company was already offering a machine of 200hp, which was designed and manufactured in conjunction with Hesston.
The story of this development work and the rise and fall of the company is warmly told by Tyler D. Hall in his book Performance/Endurance, the story of Field Queen Incorporated, which provides an appreciative account of the marque’s manufacture in Kansas, leading up to its acquisition by Hesston.
Hesston came to recognise that the Field Queen format had served its purpose over the years and a clean sheet design was required.
The result was indeed a different machine altogether although a Field Queen engineer, Ron Guinn, did have an input into its development.
Launched in 1983, it was an articulated 4WD machine that had the carried over the idea of a collection tank for the grass, as an option.
This was unloaded by a belt mechanism rather than tipping it out, which had always been a risky venture on anything but snooker table smooth ground.
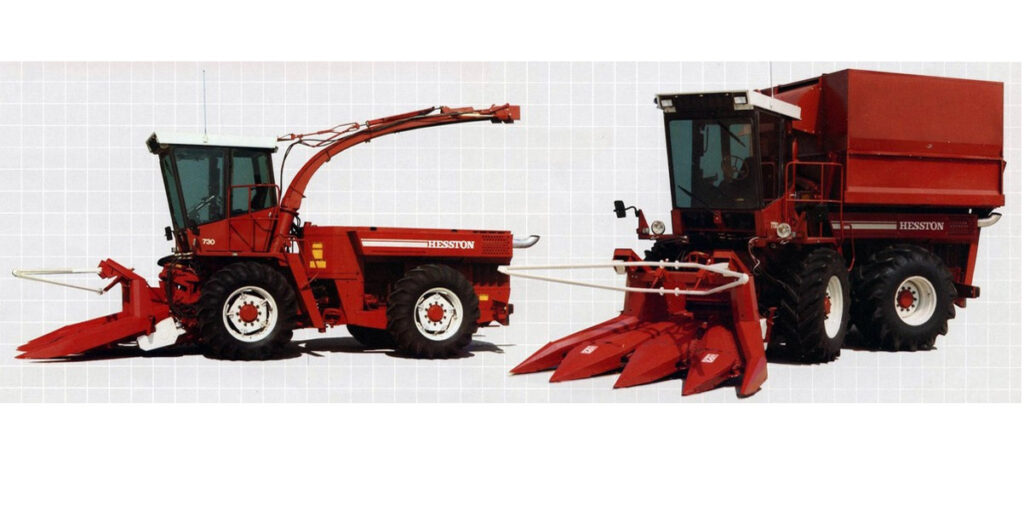
Known as the 7730 it was made in France, at the old Braud combine harvester factory, and featured 350hp Cummins engine which kept it ahead of the pack, for even the top of the range Claas 690 introduced in the same year only offered 300hp.
Perhaps it was too far ahead of its time, and although the grass box meant that it could work without interruption while trailers were changed alongside, a feature of combine harvesters, the mechanism was cumbersome and no doubt added weight and expense.
It was soon replaced by the more conventional 7725 and 7735 models. These machines followed the now standard format of blowing the grass into trailers via a spout rather than using the box and belt method, they also had the drive axle at the front with rear-wheel steer.
Catching up in the self-propelled market
This arrangement has remained as the most logical layout for self propelled forage harvesters; they have simply gotten bigger and more refined with additions such as 4WD becoming standard.
Krone adopted the same format when it entered the market in 2020 as did Fendt in 2012 and now all the major corporations have a stake in the market along with the smaller concerns.
The SPFH has come a long way over the last half century with attempts to mimic the ability of combine harvesters to keep cutting without interruption being tried and abandoned along the way.
Forage harvesters are considered specialist machines in their own right, with teams of engineers dedicated to improving their output and efficiency, but it is unlikely that we will see any radical new layouts in the near future.