Farming on Derryscollop Road in Co. Armagh, alongside his son-in-law Glen Crooks, is Robert Martin.
Many might know Glen from Instagram as ‘@the_calfman’.
The pair run a calf-to-beef system and in recent times have breached out their operations into breeding Speckle Park cattle, an enterprise on the farm which is still in it’s early stages.
The purpose, however, of Agriland’s visit, was to check out the new handling facility on the farm.
In times gone by, the duo had been handling their cattle in a standard crush. However, the task of loading and unloading cattle into, and particularly back out, the crush got more and more tedious as numbers grew.
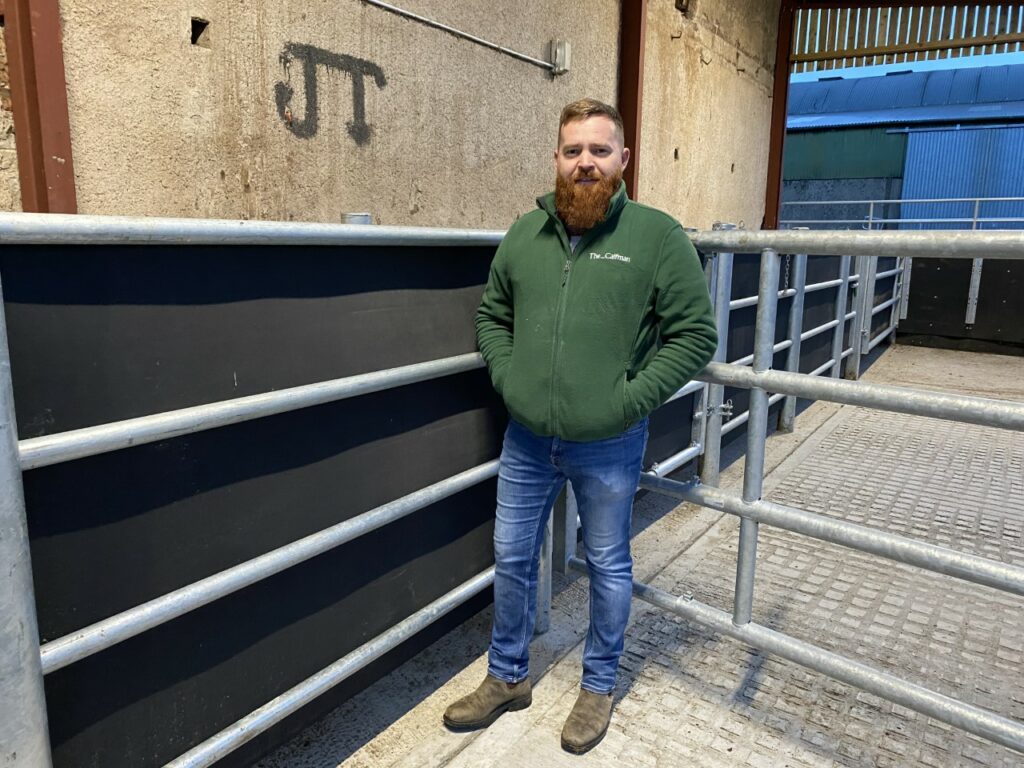
Speaking to Agriland, Glen said: “Tasks that involved having to load cattle into the crush in recent years had been put on the long finger because it was tedious, labour intensive and awkward.
“It was all three of those things [that inspired the upgrade], particularly when it came to unloading cattle out of the crush because rather than letting the cattle out at the front of the crush we had to force them out the back of the crush.
“This wasn’t too bad when numbers were small but as we got bigger and more cattle were going through the crush, it was a job you wouldn’t look forward to doing.
“So, we said we needed to look at building a new handling facility, one that tied in with the existing sheds and the new one we built last year so that it would take the hardship out of having to do jobs such as the herd test, for example.
“Furthermore, and most importantly, we wanted a safe space that we could handle the cattle. It’s designed in a way for that purpose also.”
The handling facility
The new handling facility was erected off an old existing building in the yard that had a lean-to off it.
However, this old lean-to was dismantled and a new one was erected by a local contractor. The old handling facility was out in the open and as a result, the cattle, Robert and Glen, were liable to the elements.
So when designing the new handling facility, it was a no-brainer in deciding to roof it.
Translucent sheeting was also fitted on the roof to increase the amount of natural daylight entering the handling area.
LED lights were also fitted for when jobs needed to be done, for example at this time of the year early in the morning and in the evenings when it’s dark.
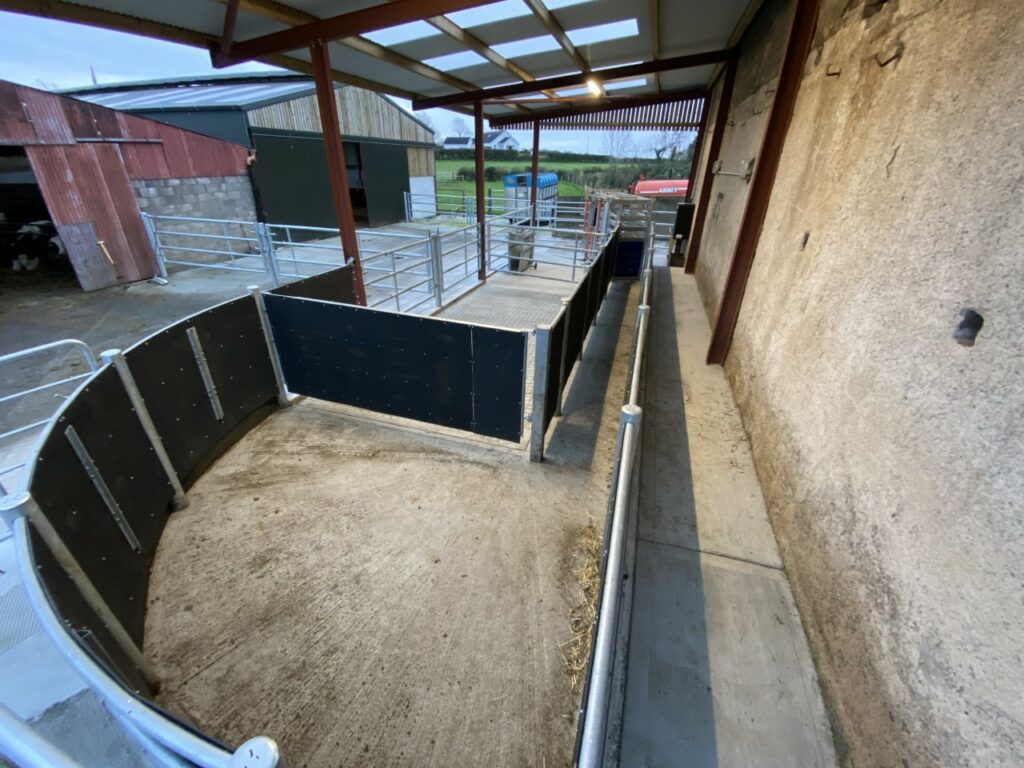
Looking at the facility in more detail, each of three sheds that cattle may be housed in can let cattle out into the holding area between the sheds and the handling area itself. (As in the pictures below of the new and existing shed).
They then can be moved into the smaller, grooved-surfaced holding area, under the roof, in the handling set up.
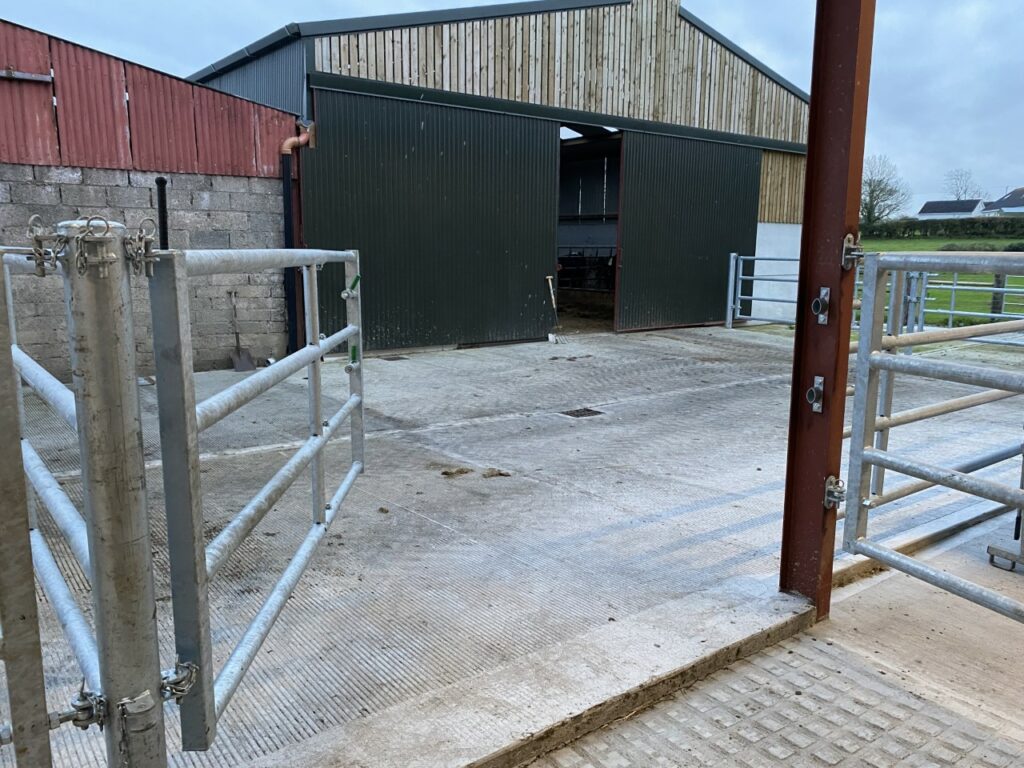
To the left of this area is where the crush is, which is separated by a four-bar gate so that any cattle that may be in the holding area can’t roam into where Robert or Glen are working and handling cattle.
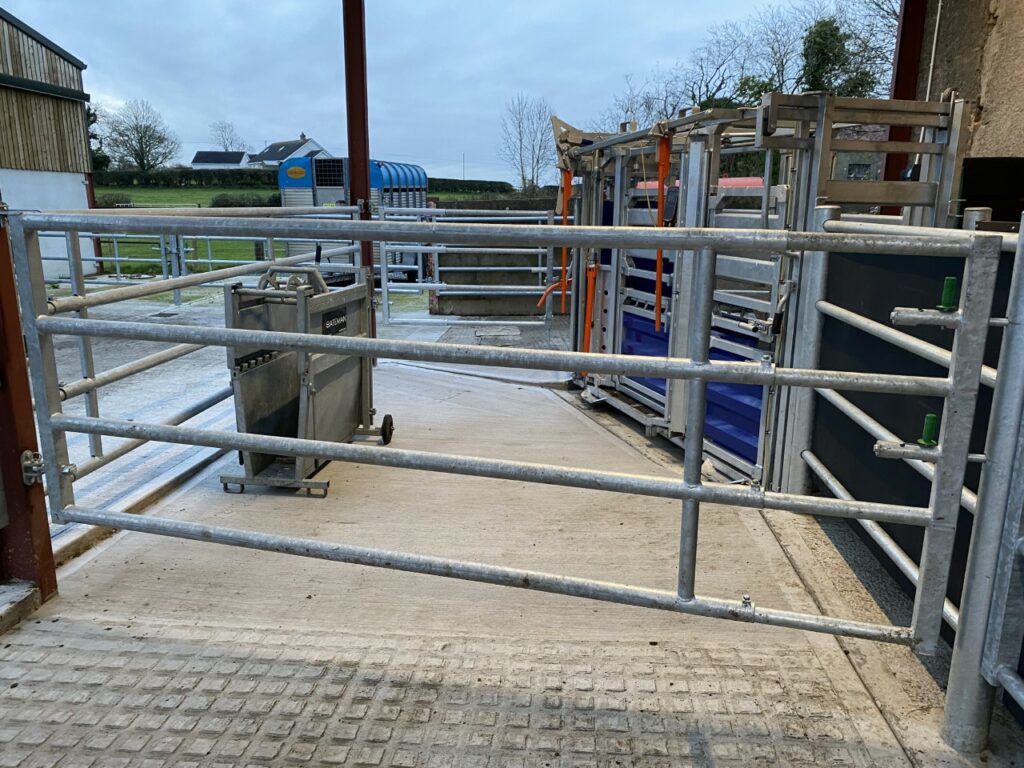
Once cattle are moved into the holding area – to be ran up the race – they make their way and congregate in the circular forcing pen, where Robert and Glen can then direct them down the race by pushing the anti-return forcing gate around fully until it locks in when all cattle are loaded into the chute.

To aid with flow of cattle up the race, stockboarding was fitted around the circular forcing pen and the entire length of the race.
Also, if the need occurred to let an animal out of the race without letting all the cattle out, Robert and Martin can do that.
Half-way up the race, a gate was fitted rather than standard bars going the length of it to allow for an animal to be let out, or if one went down in the crush.
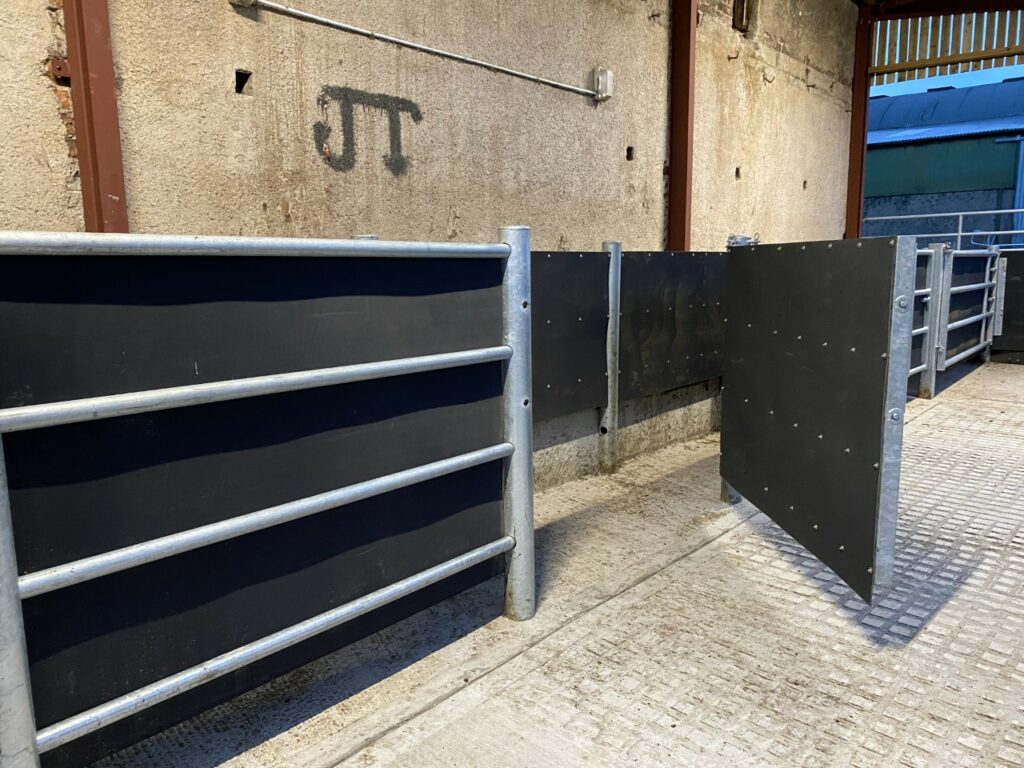
Cattle can be accessed from either side of the race, but on one side a raised walkway was incorporated.
This comes in handy, for example, in the instance of clipping the backs of cattle; you could run along the crush without having to stoop or reach in to get near the older cattle in particular.

The crush
One of the most impressive features of the handling area can be found front and centre: The Clipex HDX crush.
Coming with a range of features, it takes away the stress of handling an animal while also being able to do so in a safe manner.
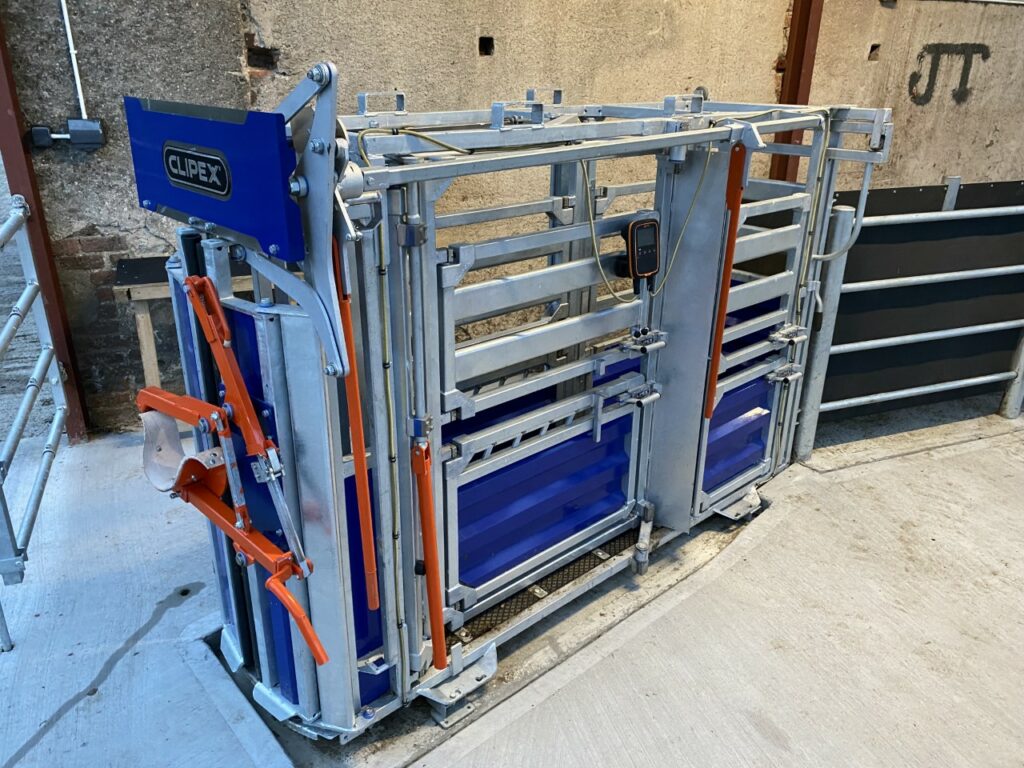
Looking to the front of the crush, it is fitted with a headscoop. Beside the handle for the headscoop is a lever that opens and closes the front of the crush. This handle can be disengaged when not in use or left as is, in position, to be able to let an animal out quickly.
There is a place between where the headscoop is and the handle for opening and closing the head of the crush that allows Robert and Glen to reach to put their hands in.
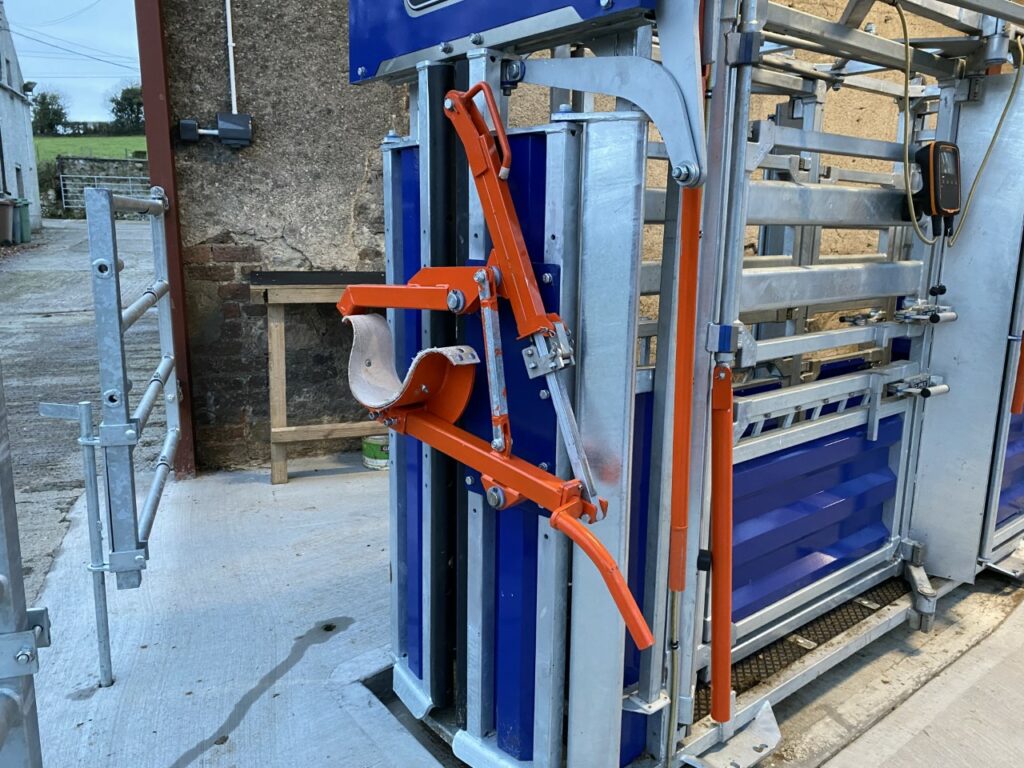
One standout feature is the fact that both sides of the crush can be squeezed in, allowing for more control of the animal as it has less space to be moving around.
It can also help to slow cattle down coming into the crush; however, this is less of a concern as the crush comes with a guillotine gate as well.
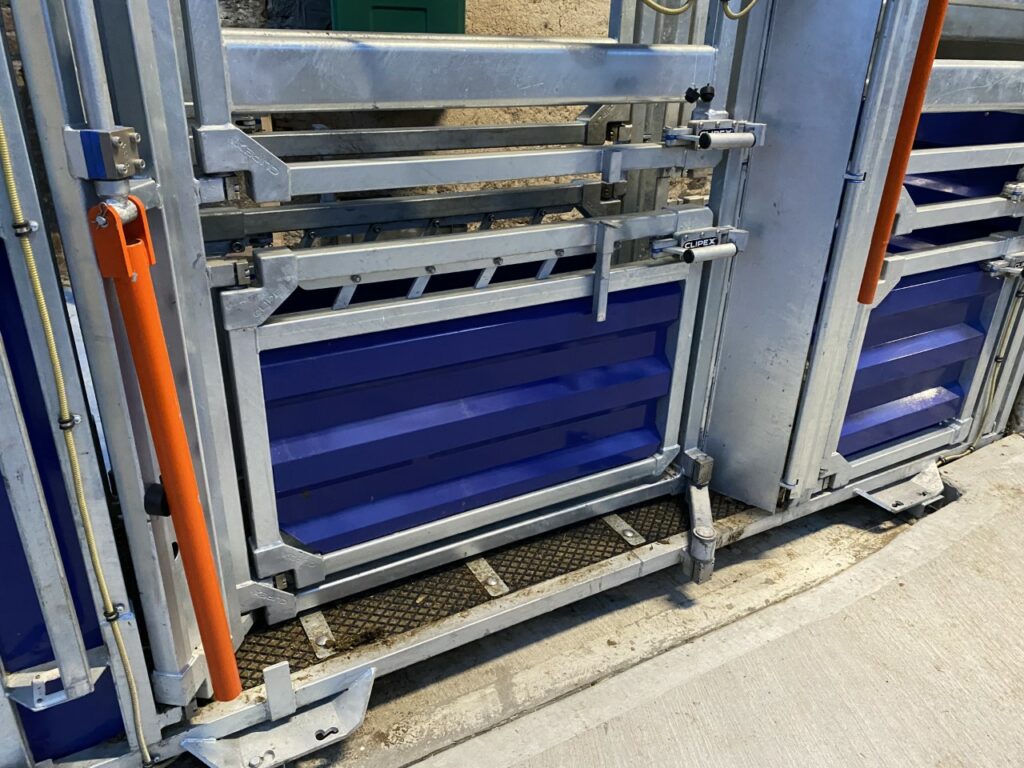
Another feature found at the sides of the crush is that the bottom compartment (the blue doors) can open out. This is very useful if an animal happened to go down in the crush as it could be let out quickly.
Or, if you were having trouble with a calf sucking a cow, for example if she wouldn’t stand for the calf to suckle.
You could move the cow into the crush and open the side compartment for the calf to come from the side of the cow as they would naturally to suckle.
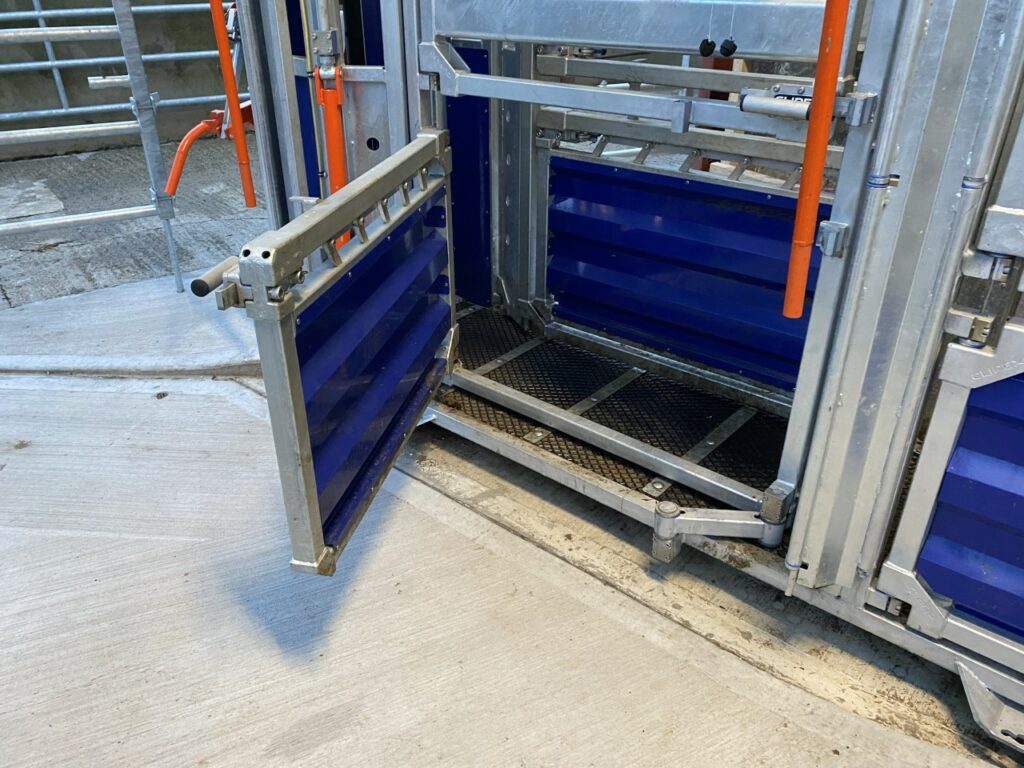
Furthermore, if the cow wasn’t standing or you just had animal in the crush that was excitable and was kicking, just above this compartment that opens up is a space for an anti-backing bar to be slipped in.
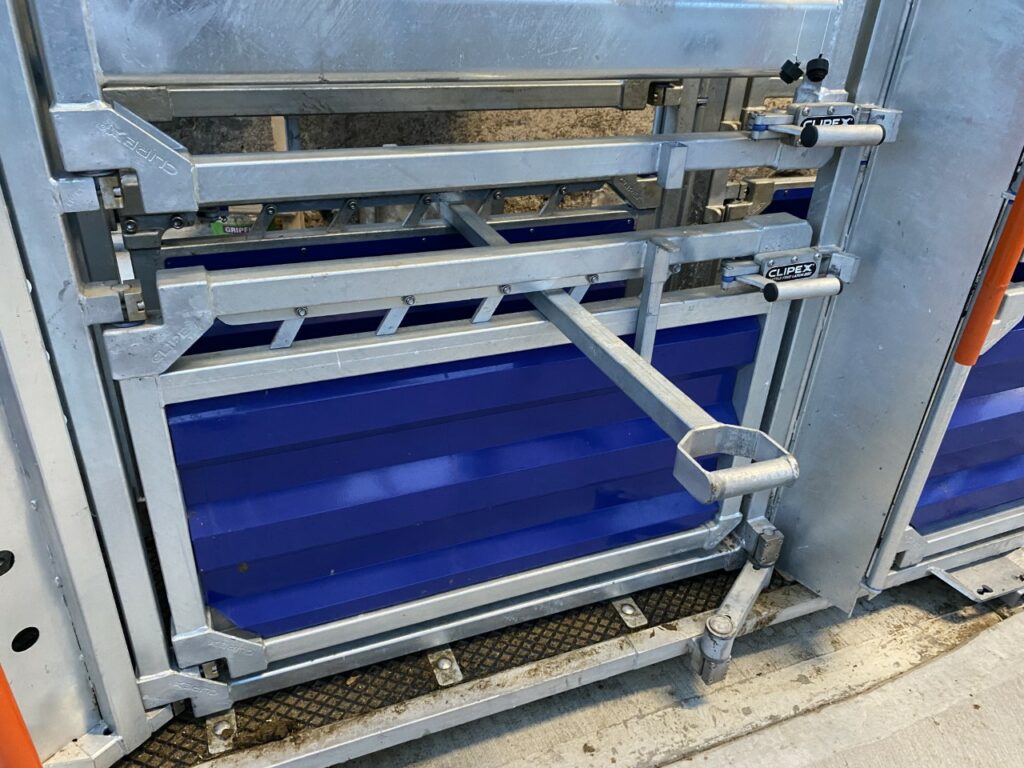
There are a number of different sections for the kick bar to be placed to suit different sized animals.
Cattle can also be weighed in the crush, which has a matted floor, something Glen will be making plenty of use of as readies cattle for the factory. The weight of the cattle can be seen at the side of the crush on the Quickweigh device.
By having the scales to weigh the cattle, Robert and Glen can track the performance across the various breeds of cattle on the farm in order to improve the genetics being used by the dairy farmers who the calves are bought from, in order to integrate dairy and beef better.
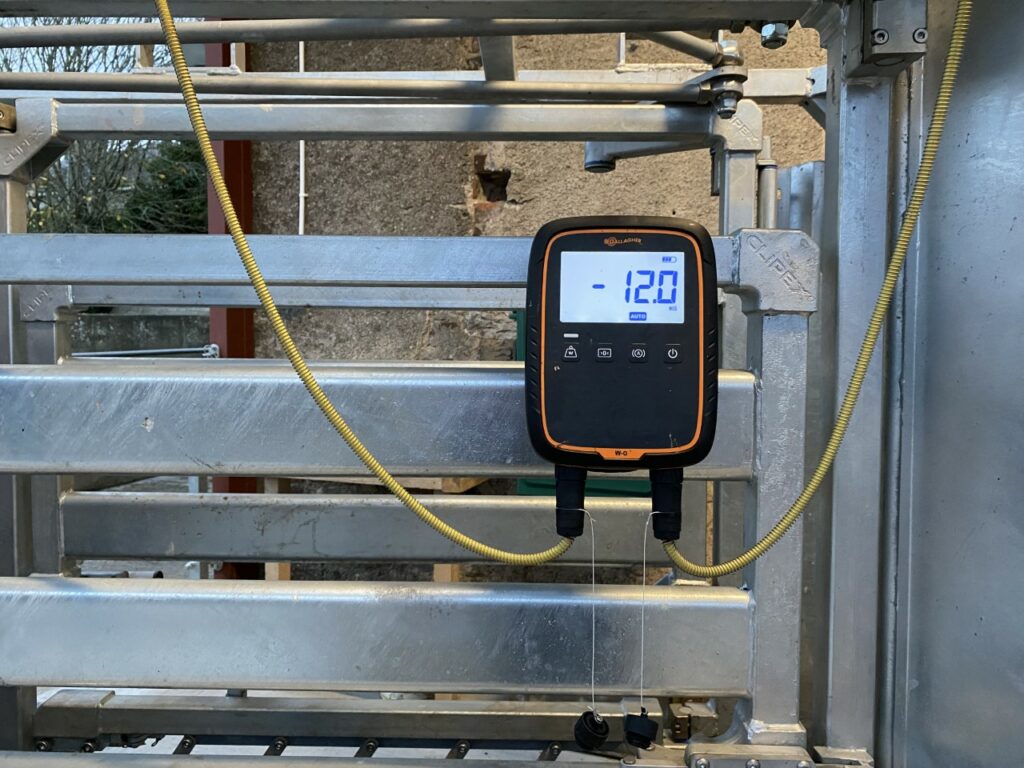
At the back of this crush is a guillotine gate, which allows for one animal to be isolated in the crush.
Once this animal is isolated, two further compartments can be opened in or out, to allow for an operator to stand behind an animal in the crush. For example, if a cow was to be artificially inseminated, she could be isolated and secured in the crush.
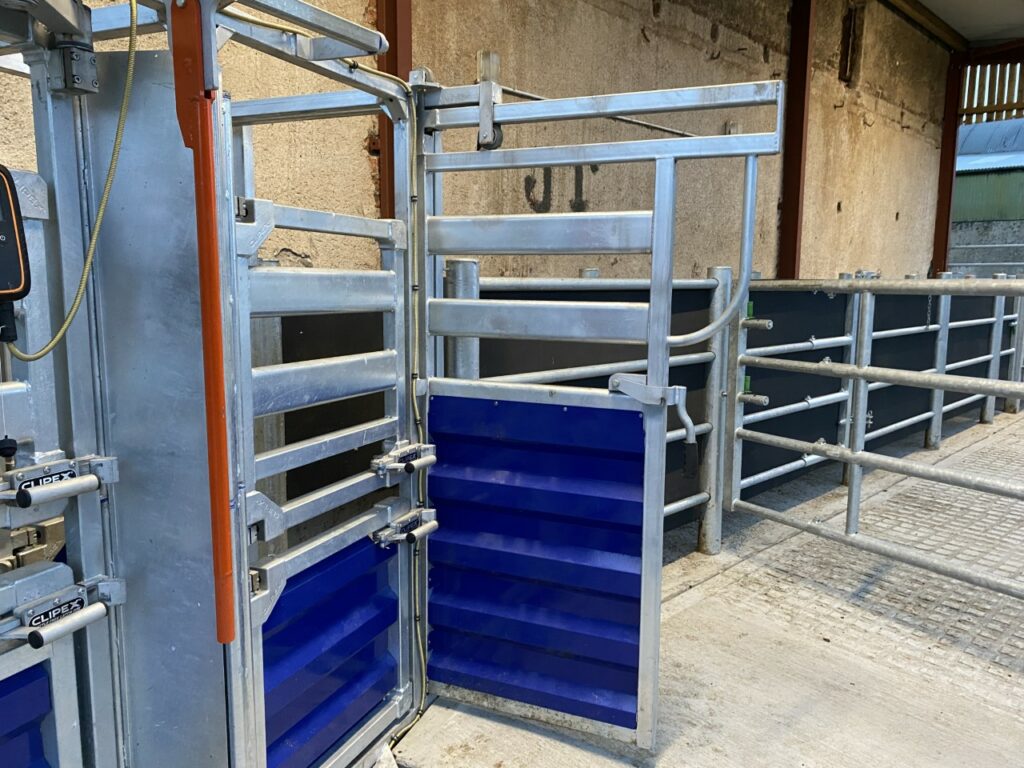
To the side of the crush on the other side, a tidy little cabinet and table were constructed to store antibiotics or any other items that would be in use while cattle are run through the crush such as a burdizzo when castrating.
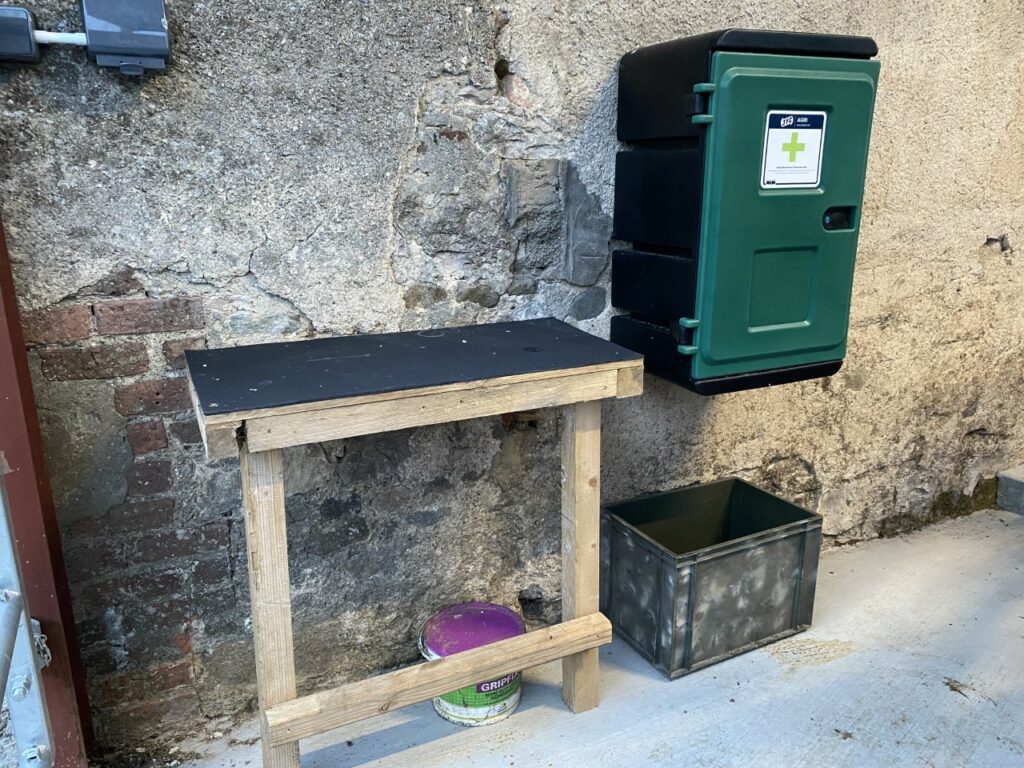
Once an animal is let out of the crush they enter back into the yard between where the handling area and sheds are before being let back into the pens in the shed.
Gates were hung either side of the front of the crush so that cattle couldn’t enter at either side where Robert and Glen would be working.
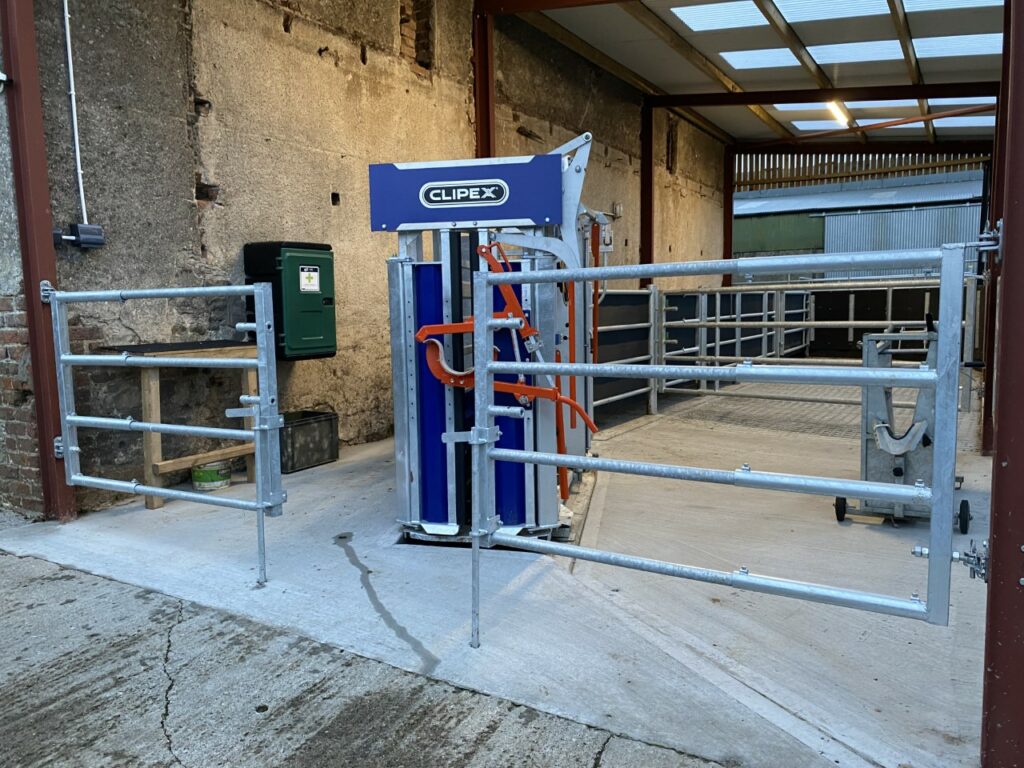
Lastly, for any calves that go through the crush, a dehorning crate can be set up at the front of the crush also to run them into.
Cost
The entire handling unit was sourced from Teemore Engineering in Co. Fermanagh. While a local contractor along with Glen erected the handling facility.
The cost of the facility is standing at roughly £30,000 all in (or just under €35,000).
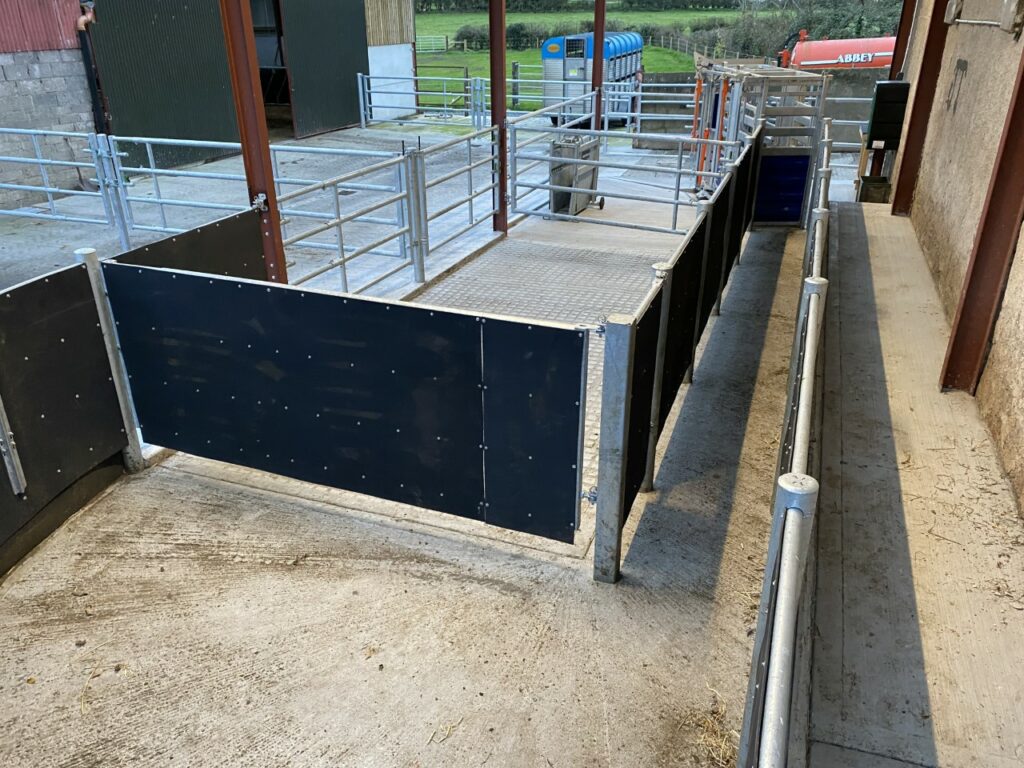
Speaking about going ahead and building the handling unit, both Robert and Glen said: “Although the time it took for example to do the herd test lately took the same time as if we were to run them up the old crush, it was still light and day.
“The ease of moving cattle from the sheds into the yard and up the crush was easy and stress free for both the cattle and ourselves.
“It was far more relaxed and the days of putting jobs on the long finger because of the old crush are over with this new handling facility.
“It’s a far safer environment to work in which is most important. We would be dealing with bulls here and they can be excitable so having a set up that allows you to handle those cattle safely is critical.
“It will take the hardship out of routine tasks and any wet day that comes, at least we will have a roof over our head,” Glen joked.
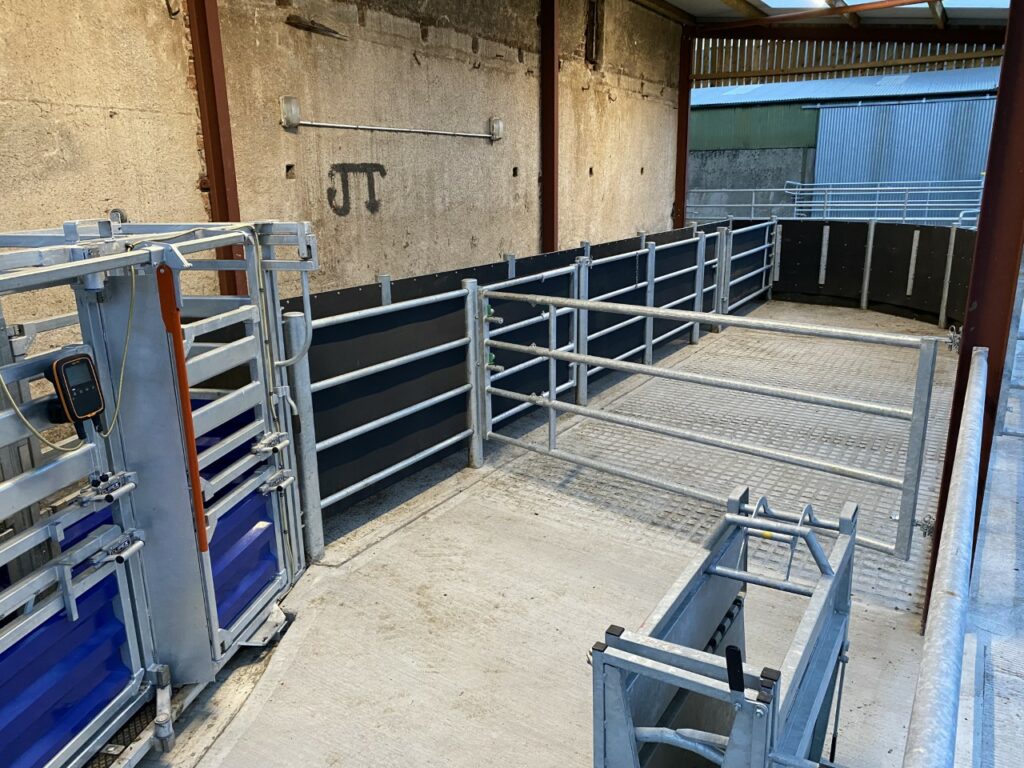