Merlo has been expending a lot of time and energy over the past year to ensure that the Irish market knows of its intentions, chief of which is to establish itself as the premier supplier of telehandlers on the island.
To this end, it recently welcomed the press to its factory in northwest Italy to show just how they go about making 8,000 machines a year, and why over 10% of the staff there are development engineers.
The first impression one gets is of the factory’s size, as it covers an area of 330,000m2 and over 90% of each machine produced is made in-house, including transmissions, axles, cabs, etc. It is only when there is no other alternative that components are bought in, with tyres being an obvious example.
Merlo workforce
The company employs nearly 1,700 people, of whom around 180 are design engineers, although not all of these work on the design of the actual telehandlers. Many are involved in streamlining and improving the efficiency of the production process.
Self-reliance is a major key to the success of Merlo. It is fully in charge of its sourcing and production of components and this extends to the installation of the production tools where it will partner with a supplier rather than just hand over the whole job to a third party.
The machining of all its metal components is certainly an impressive feature yet it goes further for Merlo, as it also forms its own plastic mouldings using an array of injection moulders upon which are mounted the company’s own moulds.
Little is left for outside companies to supply, nor does Merlo produce components for anyone else, the focus is on in-sourcing to ensure that as much of the product is made by Merlo.
Going underground
Yet what you see at the ground surface is complimented by large areas of underground storage and logistics, plus a rather unique component transport system.
Under the factory floor lies a network of railways that transport the larger items around the factory instead of having forklifts and battery-powered trucks do the job on the shop floor. This saves space while increasing efficiency and safety.
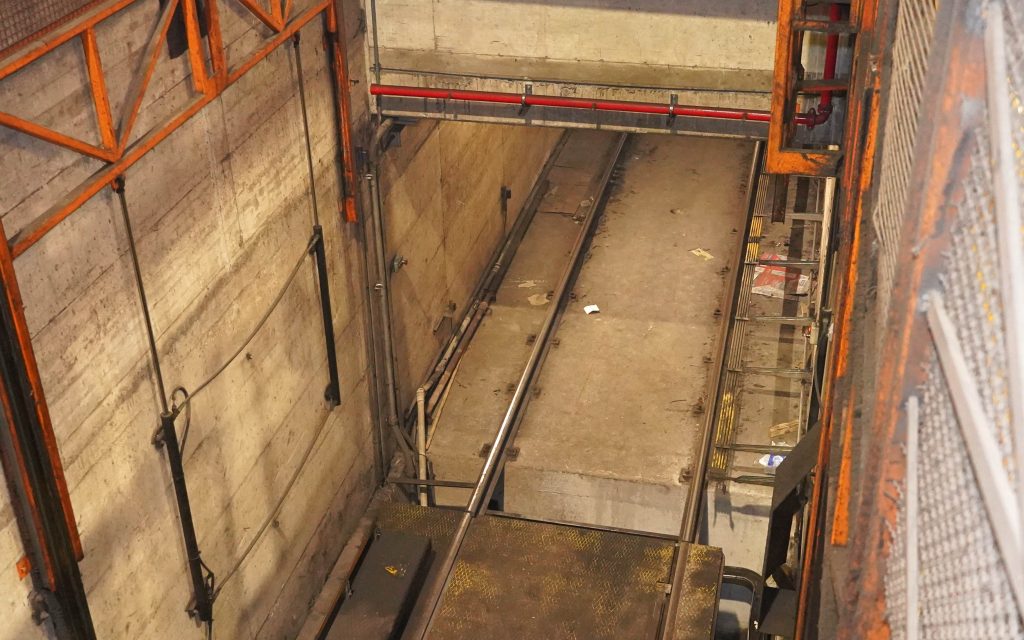
It rather sums up the approach of the company to the management of the factory. Being owned and run by the Merlo family, there is no great process to go through to get things done, the family just does what it thinks best.
This can lead to going off on tangential projects or wasting resources on ill-conceived ideas, and it may well have done so in the past, but presently it works to create a modern production facility that is not confined by standard procedures or protracted decision-making.
One area where this shines through is in the welding of the mainframe. All is done by robot despite other manufacturers insisting that teaching robots to weld a large range of major components is too expensive and time-consuming, Merlo just get on and do it.
Robots good for employment
The company also turns one of the age-old complaints about automation on its head. It is of the belief that automation actually increases employment, as it requires a skilled workforce to implement its installation and then work alongside it.
Having created the partnership between robot and human, there then exists the demand to keep it busy, and it is this which drives the company to innovate and sell more machinery, the net result being greater employment.
New staff members go through a six-week training period before being let loose on the shop floor. Assembly is no longer a question of simply bolting bits together, the parts have to be brought together with precision and checked by instrumentation as they are done so.
In-sourcing key for Merlo
Following this path of self sufficiency and reliance upon its own engineering resources has led to Merlo’s range of machines having a character of their own in that everything in the design and production process is focussed on optimising the telehandler’s performance.
There are no compromises required to be made in adapting to a supplier’s component as there are few components not designed and built within the MerloGroup.
This allows the designers the freedom to build a machine that works as a fully integrated assembly of purpose designed parts, enabling it to be built lighter and stronger.
Lightweight boom
The boom itself is a case in point. Merlo not only designed the boom but were involved in the process of creating the programme that bends the metal in the press, a piece of software that measures the resistance of the metal to deformation and so adjusts the pressure of the press in real time.
Different steels are used for different sections of the boom and for different parts of the machine in general, 70,000t of it is consumed each year.
This has meant that the booms are smaller, lighter and can sit lower in the chassis, increasing stability and giving greater vision to the right-hand side of the machine.
Merlo may at first appear like just another machinery manufacturer but there is an ethos evident within the company that raises it above the norm.
We are told that the family believes in putting everything back into the firm, and indeed, investment is to be seen everywhere, there is a constant drive for a 30% increase in productivity with each new change to the production process, an ambition which is paying dividends.