The LAMMA machinery show is opening its doors over at the National Exhibition Centre in Birmingham this week, with Kverneland introducing their latest developments to the UK and Ireland.
Kverneland has two innovations at the show, the first being Curve Pilot which involves the automatic management of the side-shift feature on Kverneland’s flagship butterfly mower, the 55100MT Vario.
Eliminating uncut strips
Now fitted as standard to the this premium machine, Curve Pilot automatically shifts both rear mowing units by up to 400mm, in response to tractor steering.
Curve Pilot does not need any GPS input or auto-steering integration to operate. Instead, it uses a simple gyroscope mechanism to sense turning movements.
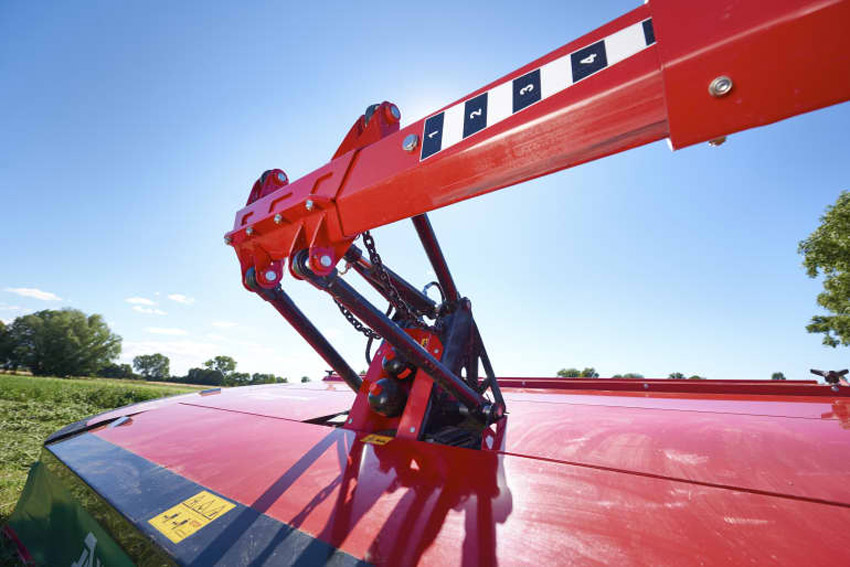
The signal generated by the unit is used to controls the side-shift on the rear mowing units preventing the leaving of a strip that can occur between the front and rear mower units when following headland curves or mowing around obstacles.
Curve Pilot enables the operator to make full use of the working width, rather than having to accept a less-than-ideal overlap on headlands for example, which restricts the working width and so reduces the overall output.
Kverneland Sync
The second item the company brings to our attention is newly developed implement gateway for all Kverneland Group ISOBUS-equipped implements.
It has been introduced to simplify and improve data exchange between the implement and the farm office.
Sync is a telematics system that has been created to improve efficiency of the machine in the field, operating with an always connected protocol through ISOBUS and a mobile network connection.
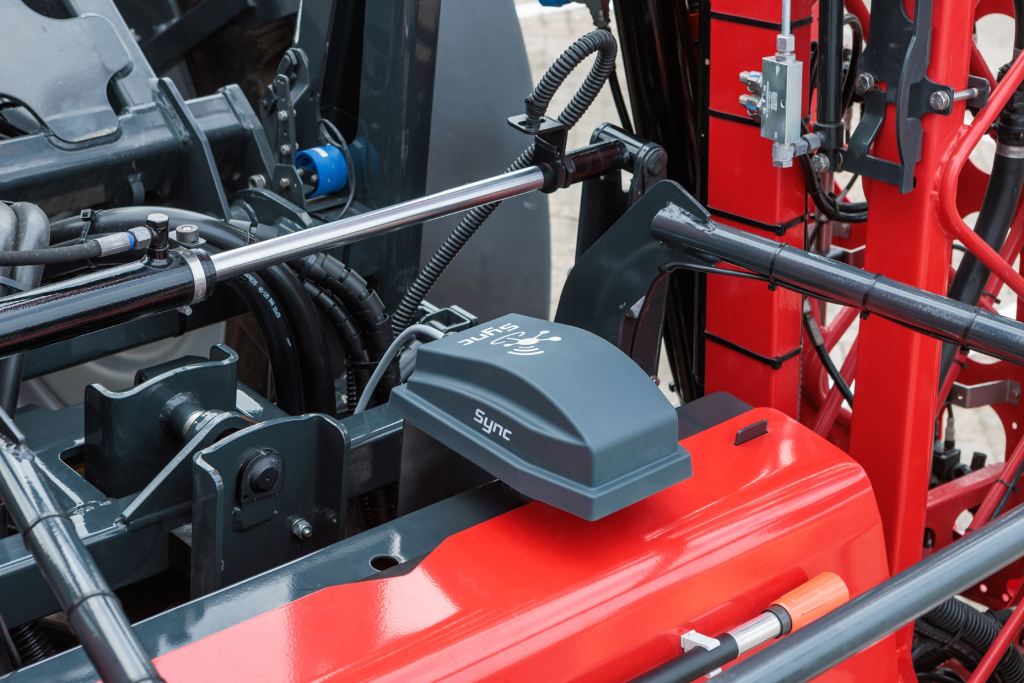
Doing so enables Sync to seamlessly transfer data from the implement to Kverneland’s integrated farm management platform IsoMatch FarmCentre.
Sync also enables real-time tracking of operational behaviour and records and alerts the machine owner to diagnostic trouble codes.
Users can also benefit from remote support through the Kverneland ServiceCentre, enabling dealer technicians to analyse data and resolve issues promptly and without having to visit the machine.
Added functionality includes synchronisation with Kverneland implement apps, one example being to establish precise machine location and tracking, and so improve the security of implements stored at remote locations.