During the 1960s and 1970s, Ford had a notable problem with its tractor engines due to porous holes forming in the cylinder bores allowing oil and water to mix, the overheating of the engine and eventually its complete failure.
The issue was commonly referred to as ‘porous block’ and engine rebuilds of the Ford 1000 series tractors kept many a dealership busy during this time, until, that is, the company got round to fixing the problem with a braced component.
Engineering challenge
Although it was Ford engines that suffered the greatest notoriety, porous blocks were by no means confined to the manufacturer, or even just diesel engines, as its cause – cavitation – provides a challenge to designers in many other spheres of engineering.
Cavitation is, as the name suggests, the forming of cavities or bubbles within a liquid due to a very sudden drop in pressure.
This generally happens on the microscopic scale and for very short periods.
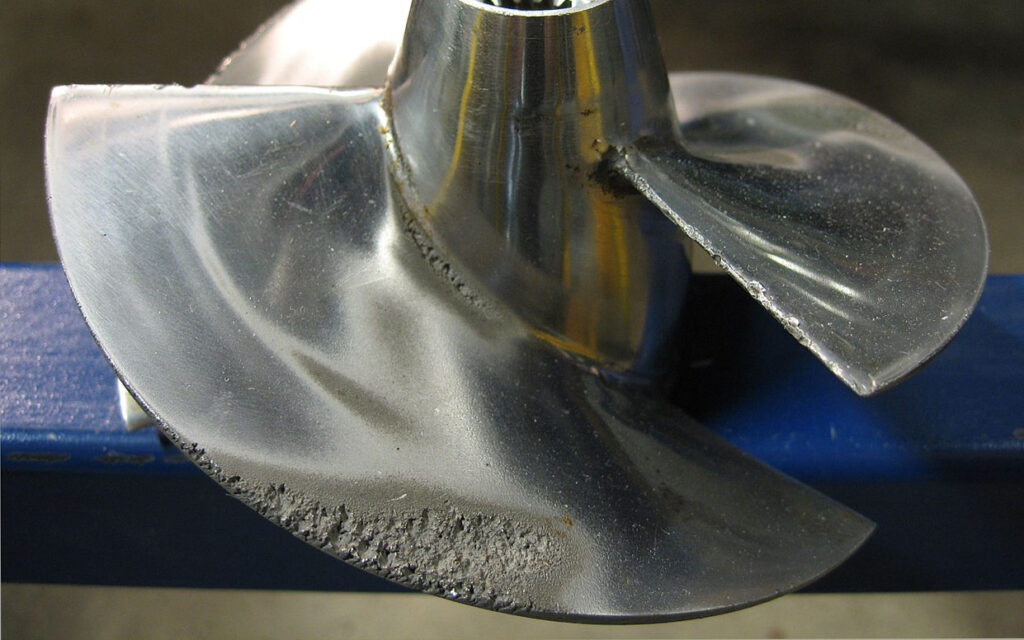
A liquid, unlike a gas, cannot expand to cater for this drop, and so it evaporates as the pressure is reduced below its vapour pressure.
The resultant miniscule cavities of ‘boiled’ liquid will then collapse as the pressure returns to normal, creating tiny shock waves that can erode surfaces over time.
It is these miniature percussions, occurring next to metal, that cause erosion of the surface which can eventually lead to holes being created that run right through a cylinder wall, hence the term porous block, although permeable would be a more apt description.
Cylinder deformation
So what is it that causes these sudden pressure drops in the water jacket that surrounds a cylinder?
The explosive force of ignition propelling the piston down the cylinder causes it to swell slightly as the piston head passes by, as it springs back into shape the pressure in the coolant surrounding it suddenly drops and the cavities form, just for an instant, but it is enough.
The problem of cavitation was well known and documented, so it is something of a mystery as to why it was not identified and corrected earlier, before even the tractors were released to the market.
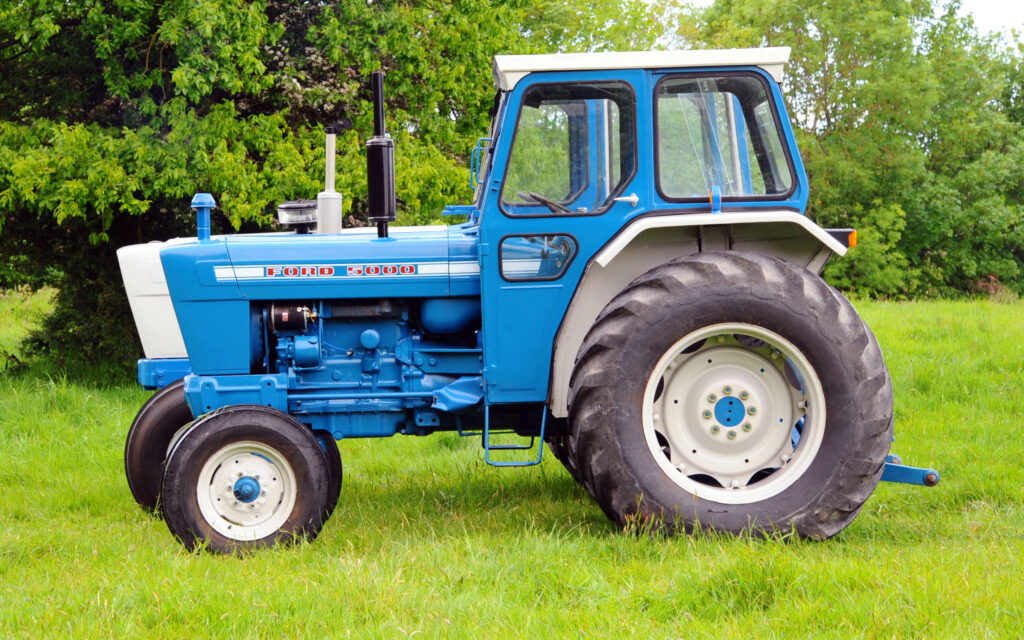
Quite what damage was done to Ford’s reputation will probably never be known, but John Deere was in its ascendency at the time and this event could have only helped encourage farmers to switch over.
Not all engines were affected; there appears to be an element of pot luck in whether a tractor suffered or not.
Four-cylinder engines are said to have suffered more than three- or six-cylinder models, and there is a suggestion that the origin of the casting may also have affected the chances of failure.
Porous block solutions
There were two main solutions implemented to avoid the occurrence of block failure. The first, and most obvious, was the reinforcement of the block itself to minimise its flexing during running and these later blocks are easily identified by the ribs or webbing visible on the exterior.
The second was to upgrade the antifreeze used, to a type which formed a sacrificial lining on the internal metal surfaces; it was this that would be degraded by cavitation rather than the metal being eroded.
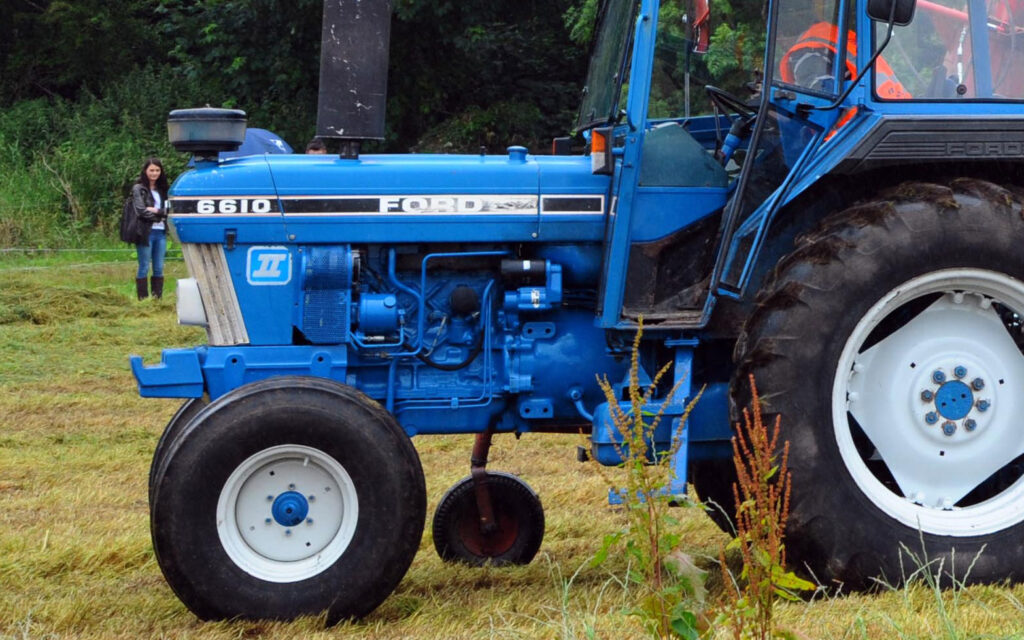
The problem has now been eliminated to a great extent although a porous block is still something to be wary of when buying older Ford tractors, and, if running them regularly, it is essential that the engine coolant is drained and replaced according to the manufacturer’s recommendations.
Despite this being a well recognised issue with the marque, especially the 4000, 5000 and 7000, there are many of these models still working half a century after they were built, so it would be unfair to dismiss these machines too lightly as they still carry a reputation for reliability and longevity which few can match.