Abbey Machinery of Toomevara, Co. Tipperary moved to its present site in 2016 and has recently added to its production capacity with an additional 10,000ft² of internal floor space.
Sales of its products, especially the tankers, continue to enjoy an upward curve and with the gradual emergence of companies back into the post Covid-19 sunlight, Agriland was invited along to have a look at the latest addition.
New assembly hall at Toomevara
The new building adds an extra 10% to the floor space on site, which extends to 30ac in all, although much of that remains ripe for future development.
The extra space is turned over entirely to final assembly rather than accommodating the range of new machine tools that have been bought in, to increase the efficiency and capacity of the production process.
These new items have been inserted into the production line rather than given the brand new room, but they are bigger than the items replaced and so have displaced other operations, including final assembly, which is why it is now located in the new section.
Greater automation was a key driver in deciding to upgrade the facilities, but this was not designed to replace staff, far from it. Welders and assemblers are still in demand and are a valued asset of the company, the idea was to move them to where their skills could be better utilised.
Lasers bring savings
The two main items that have been brought into the factory are a fibre laser cutter and robotic welding cells.
Lasers have moved on considerably from the days of slicing up James Bond, and are now firmly in the mainstream with the latest fibre-type cutters running considerably more efficiently than the plasma types they are replacing.
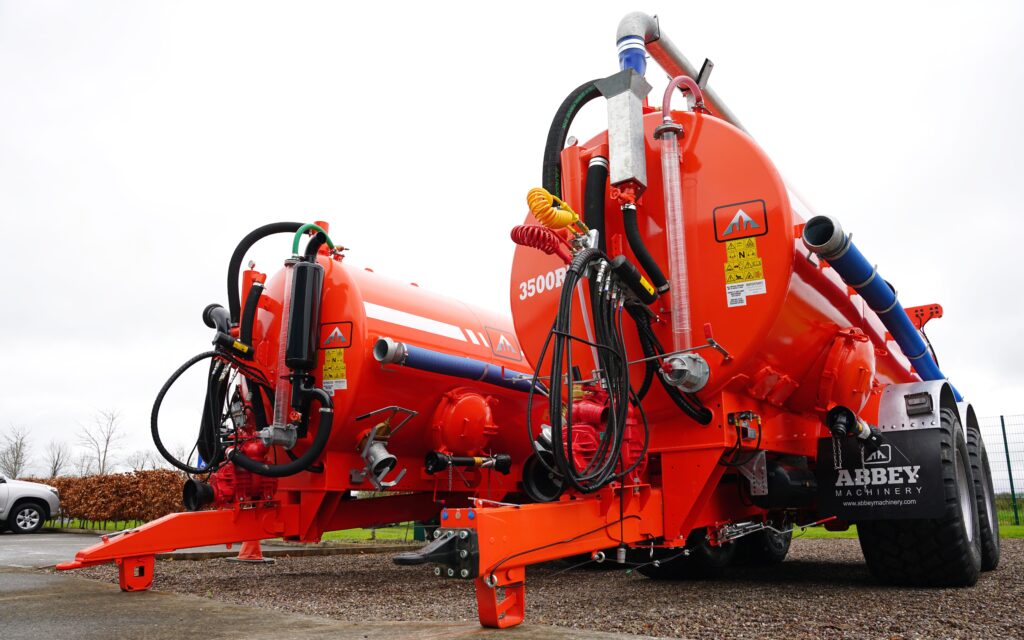
The fibre refers to the optical fibre within the head which is used to generate the cutting beam at specific wavelengths which, in turn, depends upon the rare earth metals with which they are doped.
The results of moving up to this technology are impressive; the cuts are cleaner and the edges smoother with little or no burring. Round holes, that would otherwise have to be drilled, are created with far greater accuracy than a plasma cutter could attain.
The bed of the cutter is also larger, allowing two mixer base plates to be cut simultaneously, while it is also equipped with an auto-feed system that can allow it to work up to 15 hours without intervention.
The company is delighted with how it is performing as it adds a further layer of quality as well as expediency to the production process.
Easing into robotics
If laser cutting has been seamlessly integrated into production, robotic welding requires a much longer and steeper learning curve.
The company has created a new role for an engineer to bring the benefits to the fore, but it is not going to happen overnight.
Robotic welding is at the centre of a thousand clichés pointing to the imminent redundancy of mere humans within manufacturing, but in reality, robots still struggle to cope with short runs of small intricate jobs, whereas they excel when it comes to longer runs or larger straight welds.
Most of the welding is still done by hand and a skilled welder can still match a robot when it comes to the quality of the weld produced. The machines have yet to take over at Abbey, although they are progressing.
Parts and retail
There are three main enterprises within Abbey Machinery. The first is the production of machinery at Toomevara, while the second, also based at the home site, is QParts, a wholesale sales and distribution company that sells to dealers and other manufacturers only.
Besides the stocking of parts for its own products, it carries a wide range of quality assured consumables such as plough points, baler knives and workshop equipment.
The third arm comprises the two retail outlets in Co. Tipperary, one at Nenagh and the other at Clerihan, just to the north of Clonmel.
Naturally, the bright Orange of Abbey Machinery is to be found in the yards along with Massey Ferguson tractors and brands such as Kverneland, Quicke and Prodig.
A family company still
The present company was founded in 1947 by Joseph Cavanagh, although the Cavanagh family was producing farm machinery of one sort or another from the late 1800s onwards.
Today it is run by Clodagh Cavanagh, granddaughter of Joe, and under her stewardship at Toomevara, the company has expanded steadily and solidly, not only adapting to the market but leading it, especially in the field of tanker design.
Over the last five to 10 years, the humble vacuum tanker has undergone enormous changes to the the way in which it is operated, and that trend is set to continue with the company constantly seeking out ideas to make them more efficient.
The greatest impression one is left with from a visit to the the factory is that of the air of professionalism that permeates the offices and production floor.
Clodagh has quietly put in place and retained a team that is devoted to creating a quality product that stands out from the crowd, not just because of its colour, but because it implements new ideas long before the competition finds itself having to following suit.