After an investment of €20 million in its Wolfenbuttel factory in Lower Saxony, Fendt has declared the facility now fully operational with the production of both round balers and Tigo forage wagons going ahead as planned.
During the opening ceremony, the first Fendt Tigo to come off the line, a 75 VR D, was handed over to Herman and Martiene Maalderink who will take it home to their farm in the Netherlands.
123 years of production
It was in 2017 when Fendt acquired the historic factory in Wolfenbuttel, where it was formally known as Welger Werke.
Since then, AGCO, the parent company of Fendt, has invested more than €20 million in building a facility for the production of round balers and forage wagons.
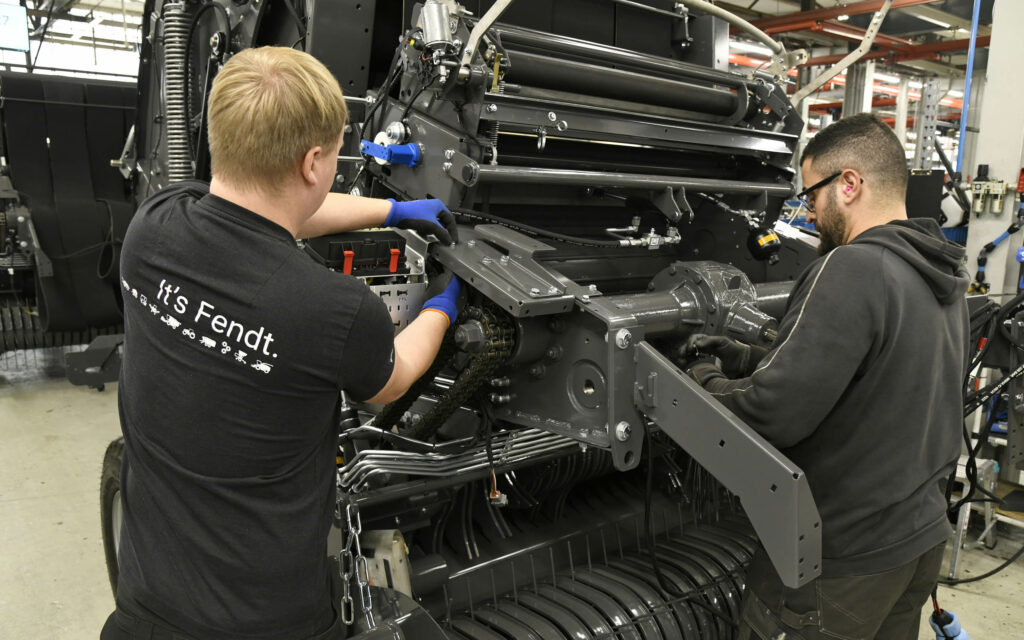
Actual manufacture of the loader wagons started in September with all models of the Fendt range being assembled in a newly equipped 4,200m² production hall.
A further 10,000m² of logistics space has been added to support the loader wagon assembly.
Moderate market for wagons
Christoph Groblinghoff, chairman of the Fendt management board, expanded upon the reasons for investing in these machines despite Claas withdrawing from the market earlier this year:
“Precisely because the market for loader wagons is manageable worldwide, we want to, and must, build the best loader wagons for our customers. With the expansion of the Wolfenbuttel site, we are investing both in a state-of-the-art development location for engineers and in a modern production location to ensure quality in development and production.”
This would suggest that he believes in the future of loader wagons as a small but steady market that is not going to grow to any extent, so it is a question of gaining market share through quality and development.
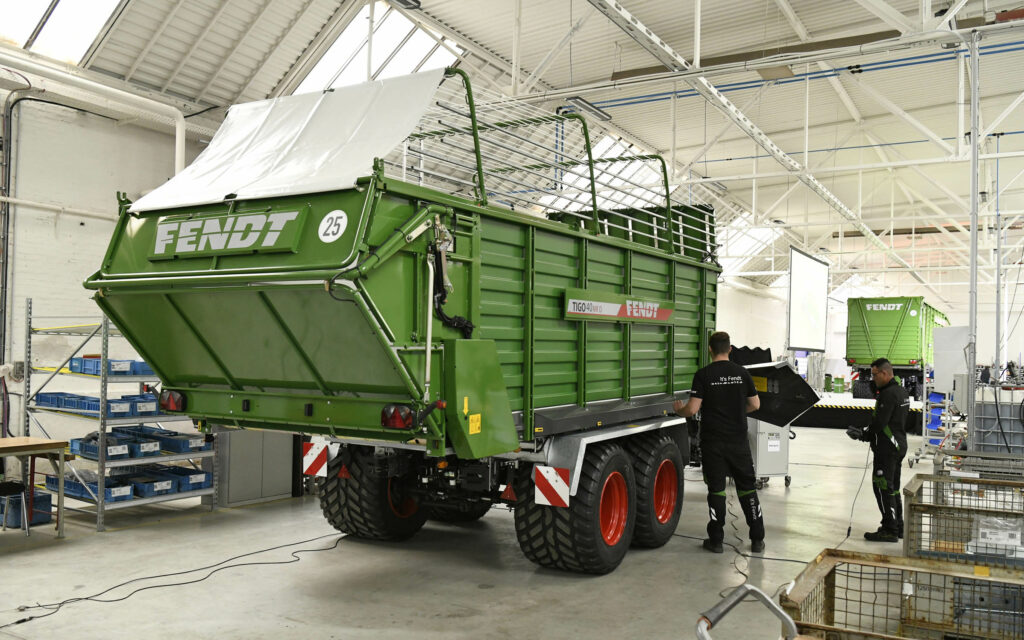
It is quite likely that other manufacturers will take the same line which may bring the danger that the emphasis on quality will make the machines prohibitively expensive, shrinking the market further.
New line brings efficiencies
The works have been completely gutted over the last three years and a new single line for the balers installed, which, through process optimisation, has allowed all the balers to be produced on the same track.
The same thinking has gone into the new loader wagon assembly line, enabling the production of a wide variety of eight series, and 25 different loader wagon models on one line.
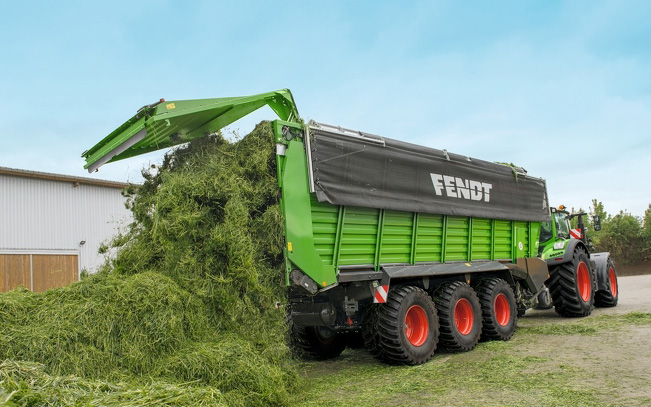
The investment has not only increased the total production of machines from the site, but has also created employment for a further 60 staff members.
A new LED lighting concept with motion detectors and a switch to chrome-free paints contributes to more sustainable production.