Getting to grips with the Alstrong Aerator requires something of a shift in perspective, for it is far more than just a spiked roller and, contrary to most implements of this type, speed is of the essence.
If it is considered as just an expensive way of poking holes in the soil then that is to misunderstand its action for, when driven hard, it becomes a fully fledged soil engaging implement that has an effect up to 30cm deep.
Compaction busted
That effect is to fracture the soil and create fissures which allows air to penetrate below the compacted top layer and well into the root zone, while allowing an easier passage for water to drain from the surface.
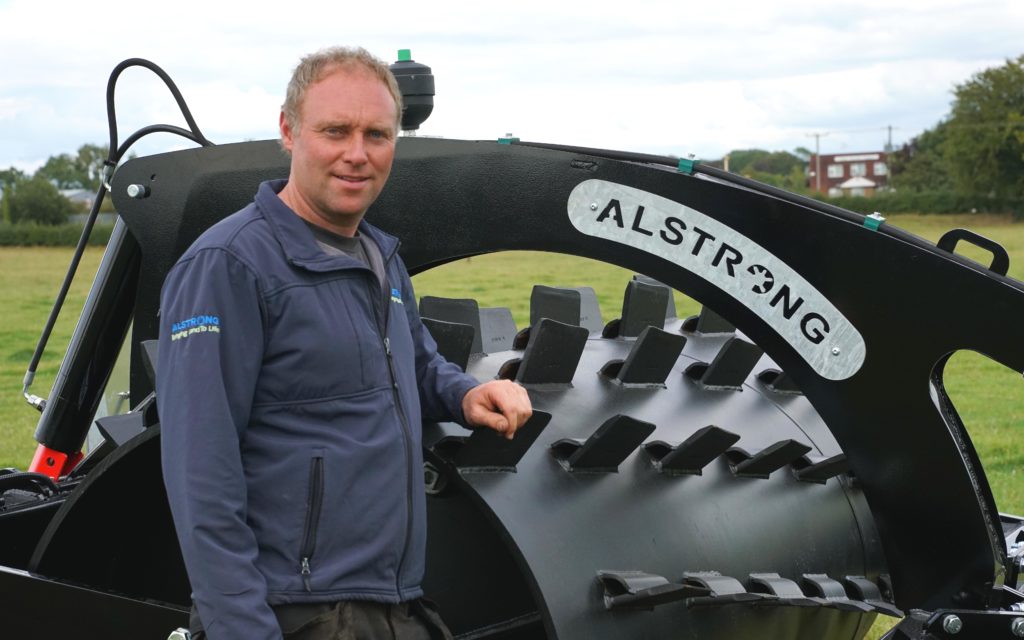
While we tend to think of pasture as being less prone to soil compaction than tillage ground, Alan Winters, founder of Alstrong, points out that cattle are the worst at compacting the top few inches of soil, especially when intensely grazed.
Field operations such as slurry spreading or silage harvesting just add to the damage he notes, and so regular servicing of the soil is important to keep it working at its best.
Total coverage
Alan believes that the implement he has developed and brought to the market over the past few years does just that by rapidly inserting a blade into the ground which causes the compacted soil to fracture, while leaving the sward intact.
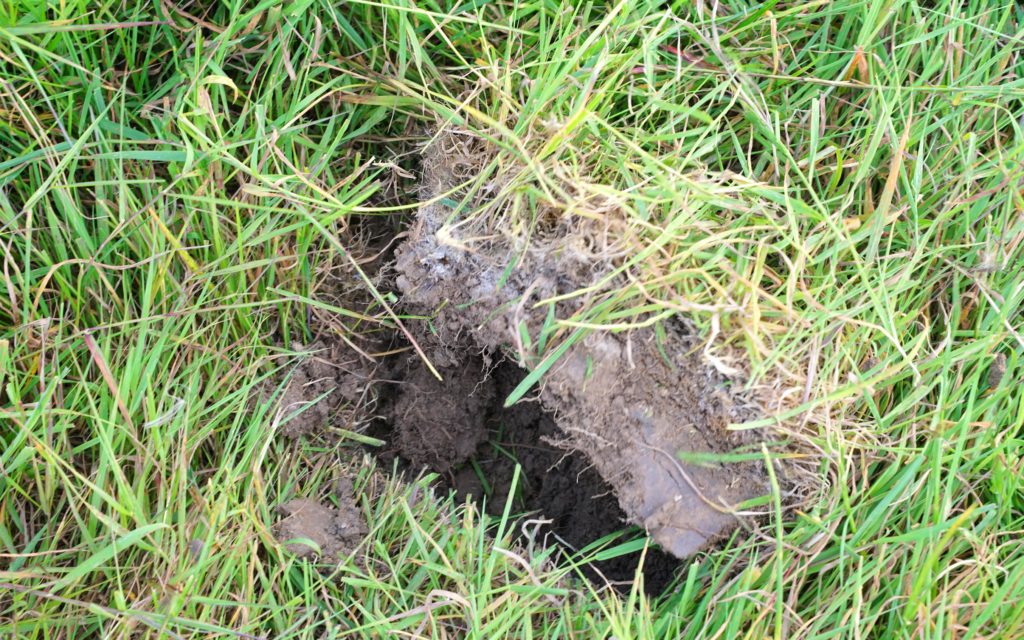
This, he insists, is a quite different action from gently pushing a spike or lug into the soil in the hope that air will have a better chance of getting to the roots.
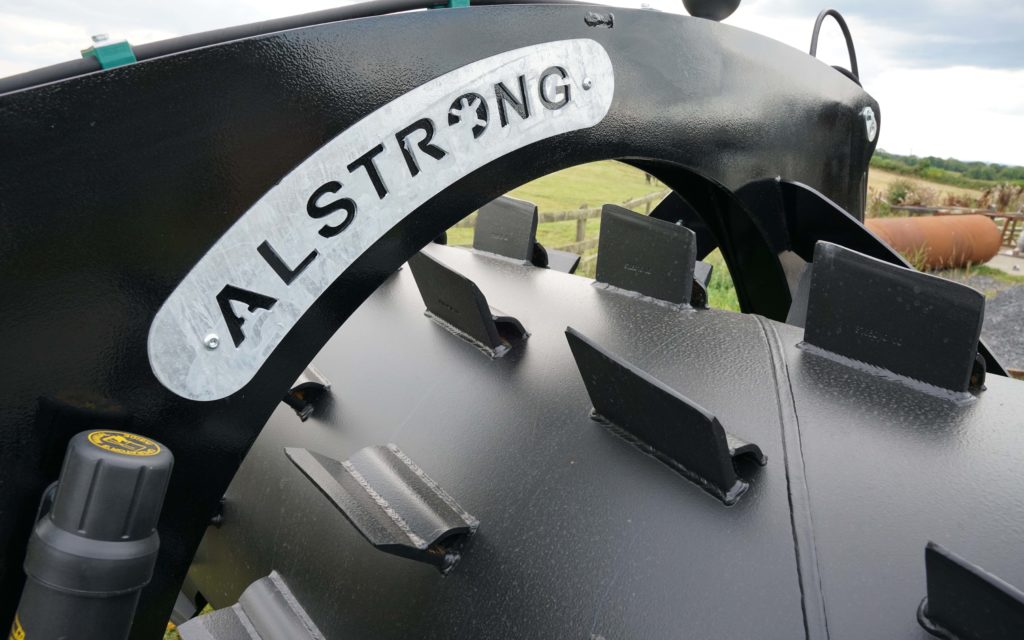
In such a scenario the effect is limited to the area immediately surrounding the insertion point. The Alstrong Aerator cracks the soil in between the insertion points and so all the ground is treated rather than that immediately next to the hole.
It also causes fissuring of the ground from the top down rather than from the bottom up, as a subsoiler would do, meaning the greatest amount of cracking occurs in the compacted layer.
Alstrong heavyweight
Weight is also an important consideration. The heavier the machine, the greater the effect, and so there is no skimping on steel in its construction. When dry, it weighs 3.5t, by ballasting the roller with water another 2t can be added.
The Alstrong aerator has the greatest effect when the soil is dry, yet that does not preclude its use at either end of the season.
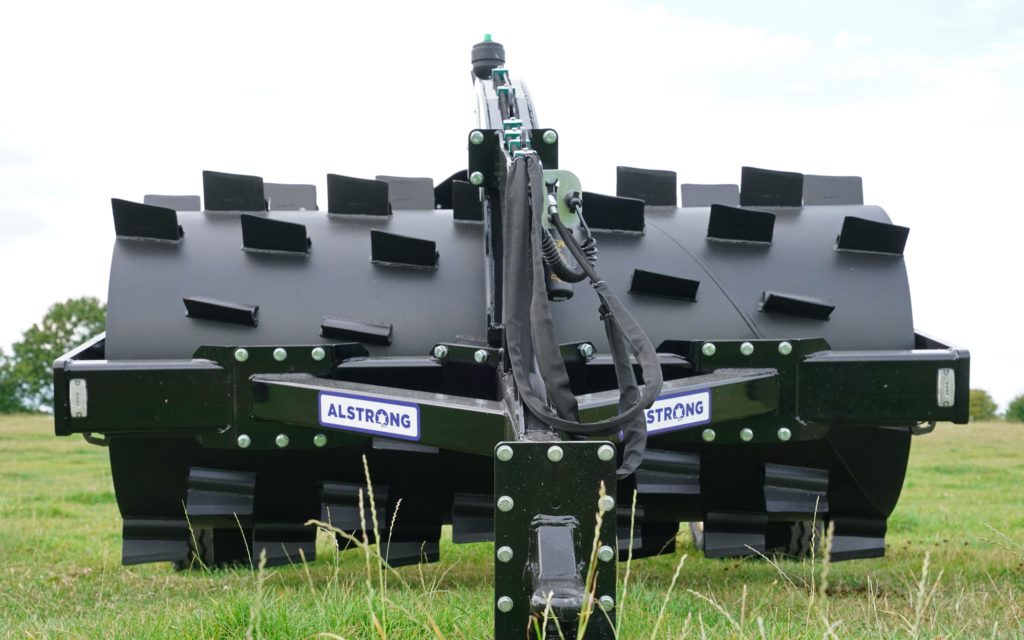
Alan suggests that fields are are treated three times a year. The first is just before slurry is spread as the slits will allow it to seep into the ground rather than off the surface.
The second is after first cut silage when the ground is most likely to respond to the treatment, while the third is much later in season to repair the damage inflicted over the autumn grazing period.
Rapid treatment
This might sound a rather extravagant regime but he does have customers who undertake it every year with worthwhile results.
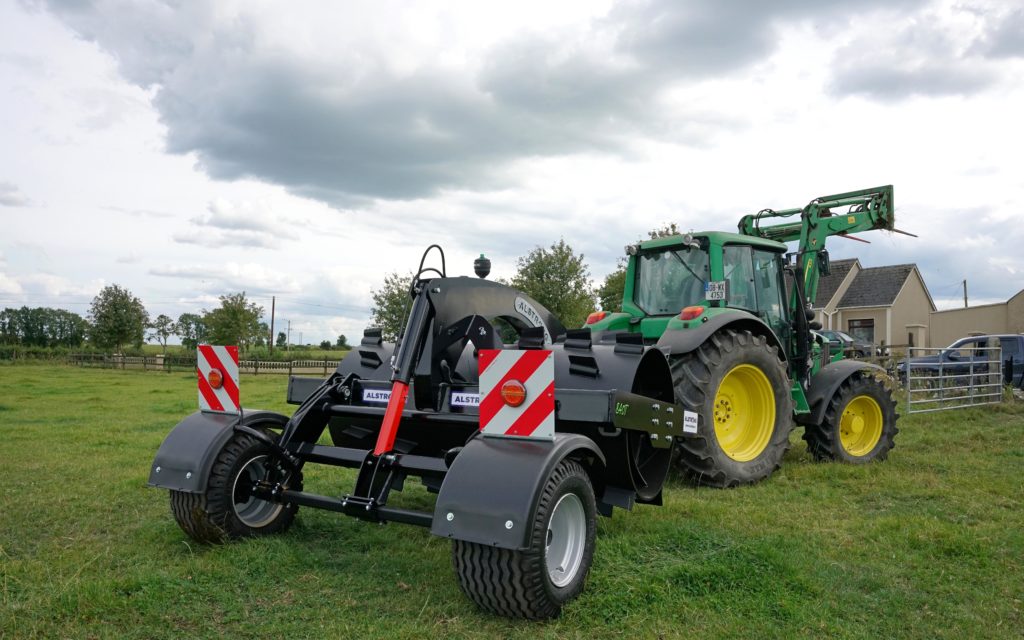
One reason why it can be done so often is that it is a reasonably quick procedure. The best results are achieved with a speed in excess of 10mph (16km/h).
At this pace the 3m machine will cover 9-10ac per hour, two day’s work on a 160ac farm with a large enough tractor, which is recommended as being of at least 120hp, or 150hp to be quite sure on uneven ground.
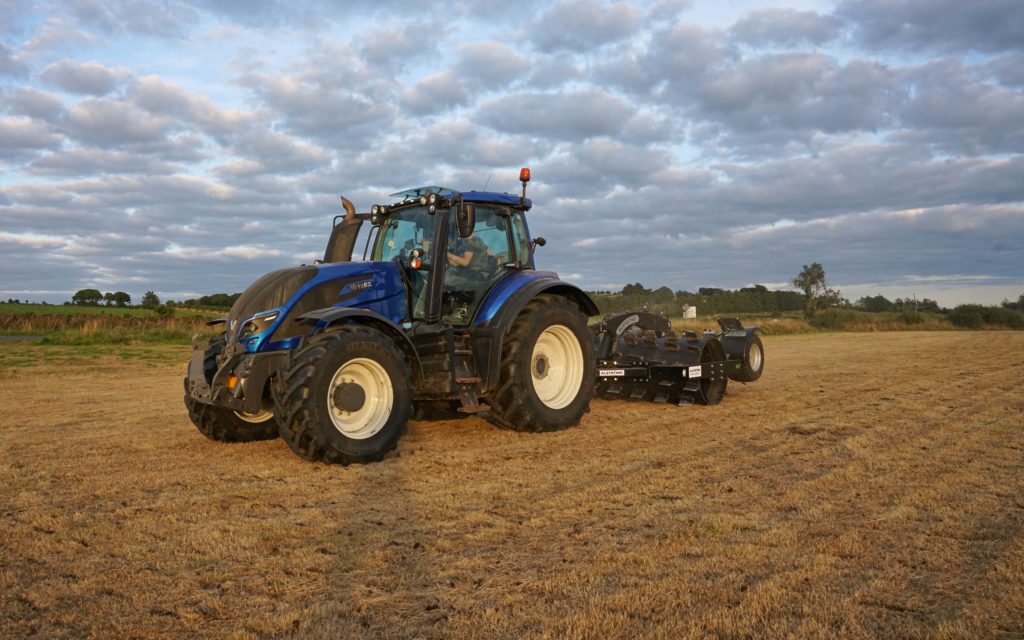
This is obviously far in excess of what would be demanded by a flat roller, reflecting the fact that it is working on the soil rather than merely squashing the grass.
Ensuring penetration
The aerator is producing 14 cuts/m², the blades are 15cm high, which all adds up to a hefty draught requirement at a speed of over 10mph.
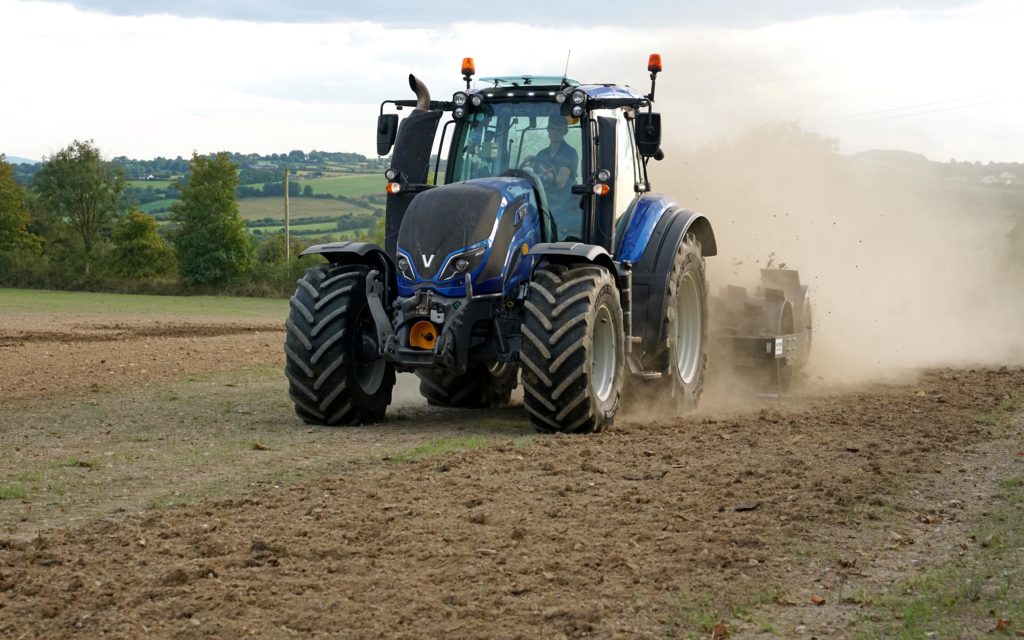
It might be thought that once having set the machine in motion it would take a good deal of effort to stop it, but Alan notes that it will stop the tractor just as soon as you take your foot off the throttle.
To ensure there is the weight available to penetrate the soil at speed, plenty of steel is incorporated into the implement. The roller itself is of tube with an 18mm wall while the end plates are 10mm and the frame sides 30mm thick.
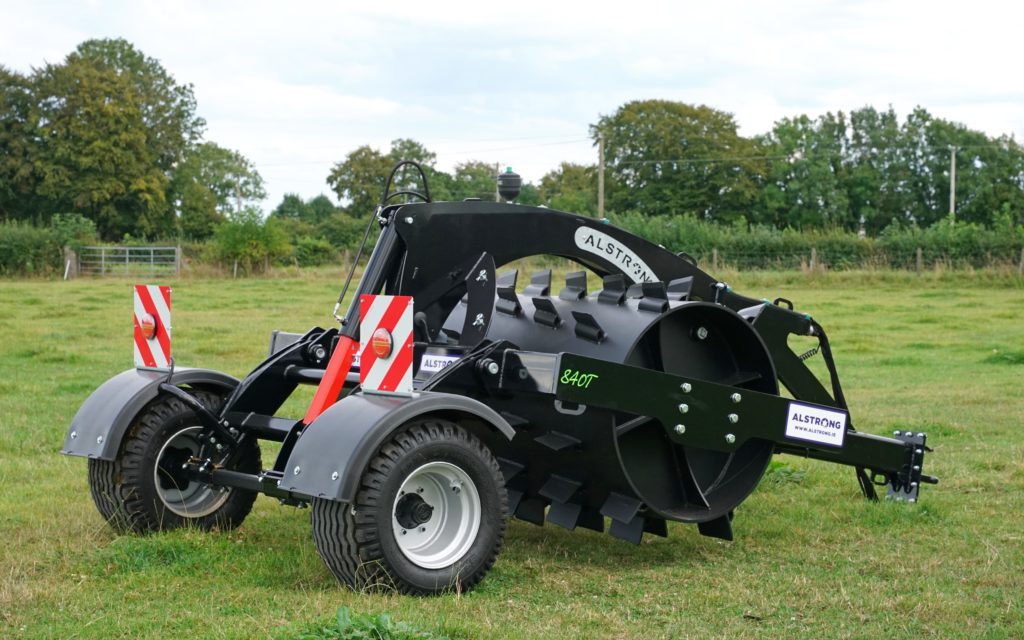
The patented blades are of high boron steel and come with a lifetime guarantee against breaking, and so far, Alan has had to replace just two items altogether.
Nylon bearings by Alstrong
Another point of interest are the bearings for the roller. It was felt right from the start that steel ball or roller bearings would simply not be up to the task of absorbing any shock caused by hitting hidden rocks, so nylon sleeves are shrunk into the bearing housings instead.
If regularly greased these should provide a long service life and so it has proved, with no known problems out in the field.
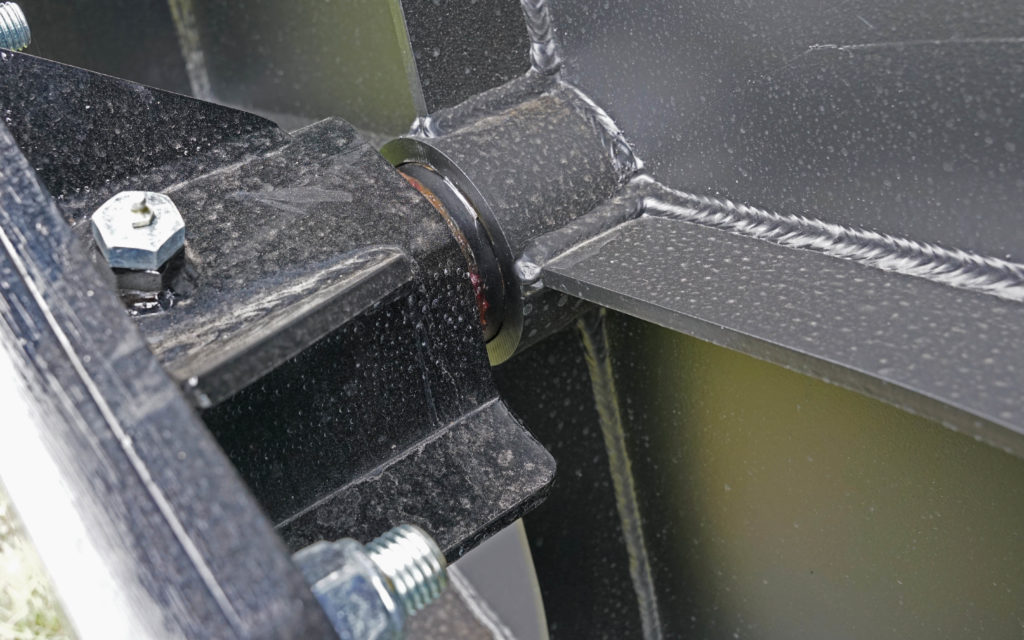
Other than the wheels and ancillaries such as light fittings, the Aerators are built entirely in-house.
Alan served his apprenticeship in fabrication and turning, with a nearby construction company, and it was being laid off in the recession that motivated him to make the weekend job full-time.
Coupling this ability to create from steel with the frustration of a local contractor who was having problems with subsoiling, brought about the invention of the aerator.
Blade positioning is key
Most of the design time was taken up in optimising the size, angle and placement of the blades on the drum, getting this right was critical to getting the machine working properly.
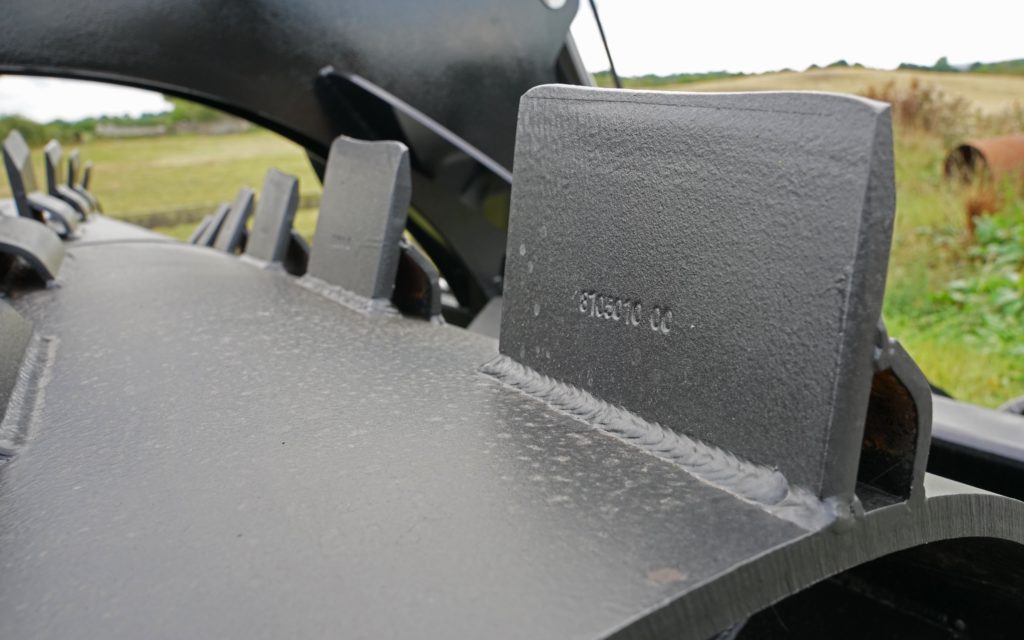
However, each needs to be welded on separately and so far, he has not yet hit upon a method of fixing them on without this labourious task.
Finding welders to do so is also difficult, with local food processing and pharmaceutical companies paying very competitive rates.
In addition to the Aerator, Alan has also developed an innovative paddock rejuvenation implement, known as the Auctus, which Agriland will be covering in the near future.